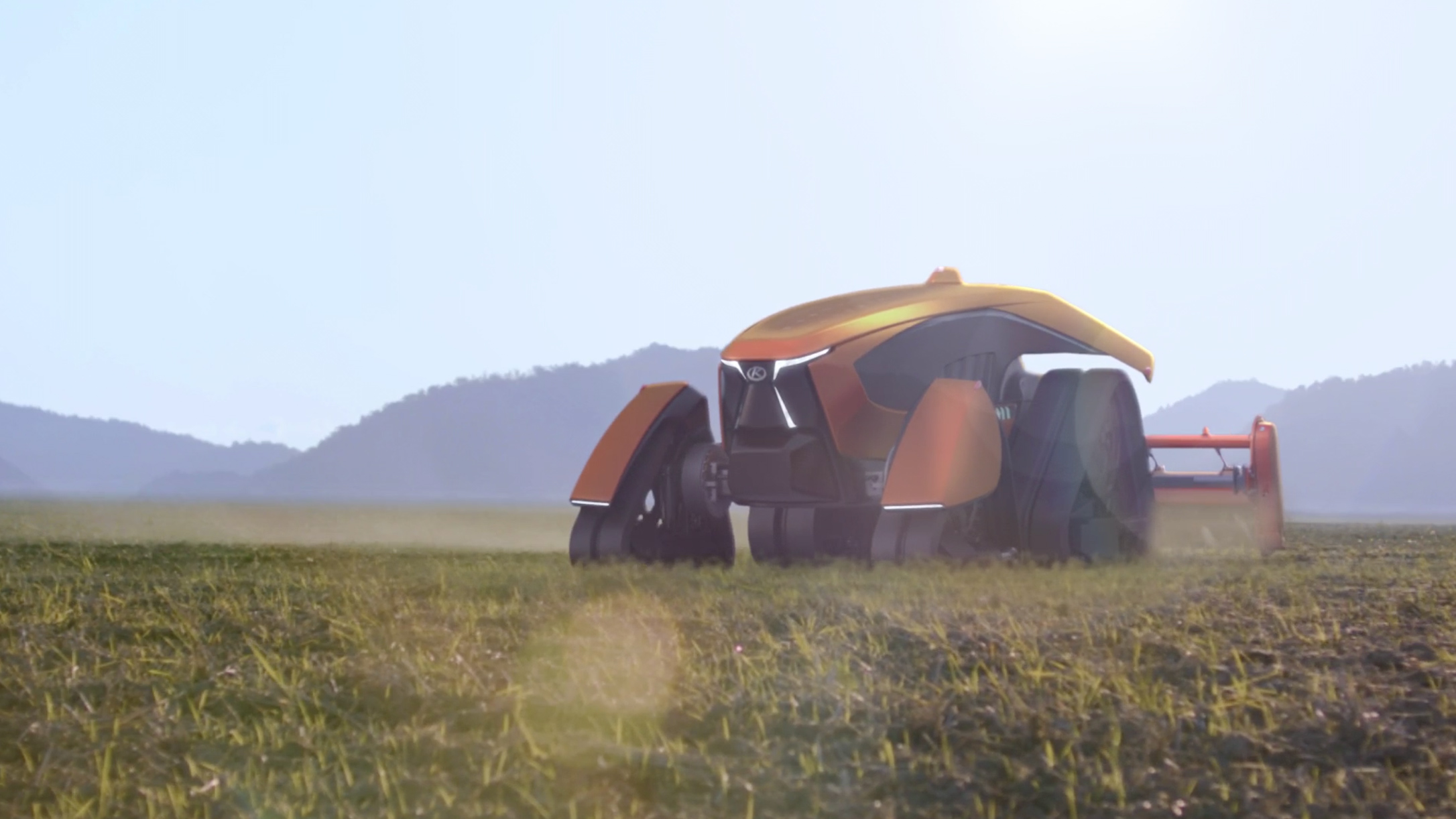
In October 2020, Kubota launched a strategic partnership with American semiconductor manufacturer NVIDIA Corporation. One of Kubota’s initiatives for enabling smart agriculture is ultra-labor saving based on automated and unmanned agricultural machinery, and the roadmap for this initiative has three steps. For Step 2 is “automation and unmanned operation under monitoring by people,” all three machines (tractor, combine harvester, and rice-transplanter) have been released. The partnership with NVIDIA marks Kubota’s efforts toward Step 3, “completely unmanned operation.” What benefits will result from this collaboration with NVIDIA, which has earned tremendous response throughout the world? And what kind of world will Kubota's vision of automated and unmanned agricultural machinery bring about? In this article, we will take a closer look at the efforts toward Kubota’s vision.
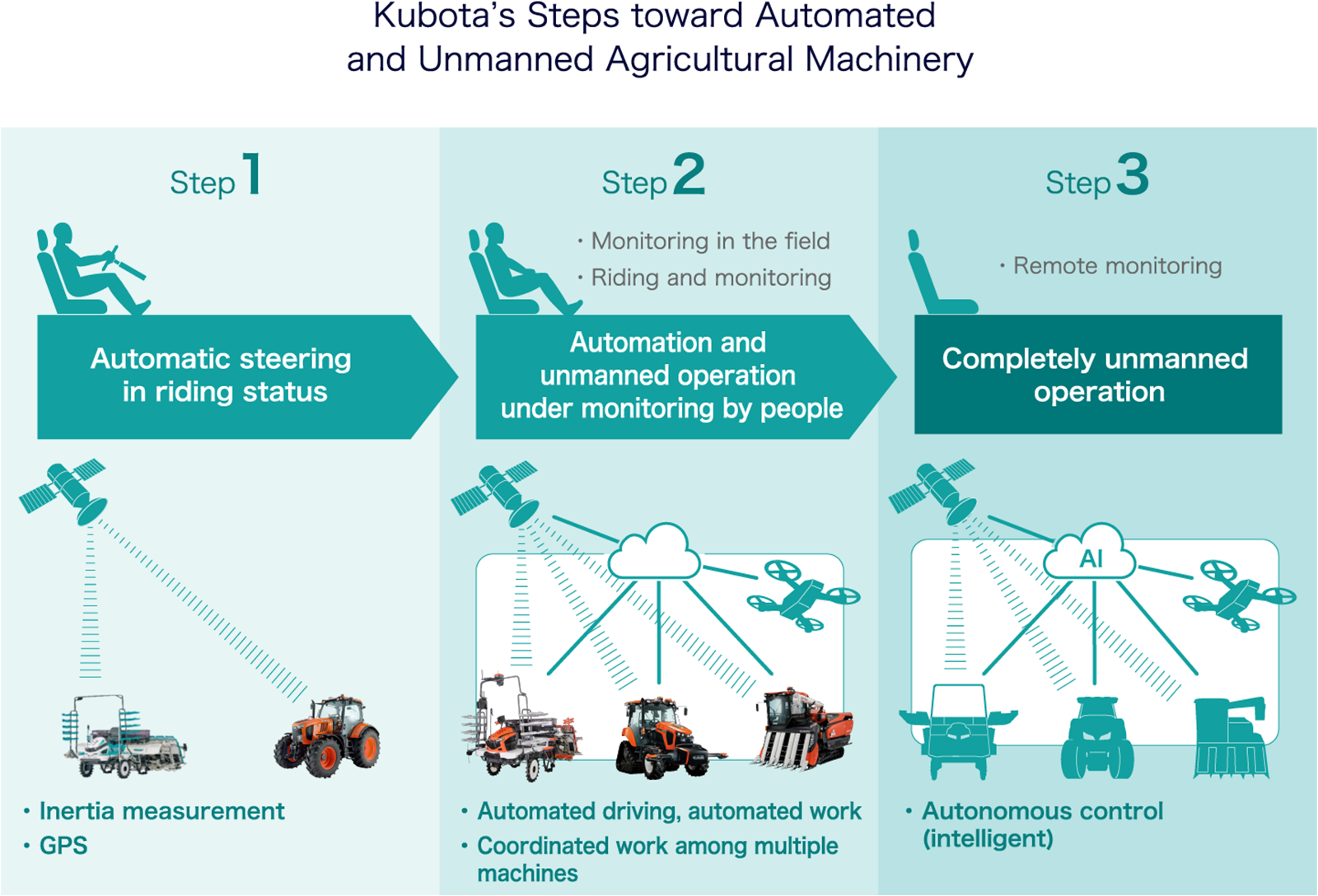
NVIDIA’s Latest AI Technologies are Ideal for Automated Driving
NVIDIA, the company with which Kubota signed this strategic partnership, is a California-based semiconductor manufacturer known worldwide for its industry-leading GPUs*1 with outstanding computational processing power. Unlike companies such as Google, Microsoft, IBM, and Amazon, which provide cloud AI that mainly performs processing on servers, NVIDIA is involved in end-to-end AI platforms, a feature that was determined to be ideal for Kubota’s approach to automated and unmanned agricultural machinery, leading to this partnership.
- *1.Graphics Processing Unit: An electronic circuit for advanced image processing provided by NVIDIA, which developed the technology in 1999. It offers advanced levels of parallel computing performance and is used for AI as well as scientific and technological calculations. In recent years, it has functioned as the brain of computers, robots, and autonomous vehicles that can perceive and understand the world around them.
An end-to-end AI platform incorporates built-in machine learning models that utilize AI to perform analysis and reasoning comprehensively for problem-solving. It features artificial intelligence that can work just like a human brain, figuring out the best way to deal with a problem from the information it learns. The NVIDIA end-to-end AI platform that Kubota has adopted provides both ultra-fast computers for AI learning and an Edge AI system on-board its agricultural machinery that enables AI inference using high-performance GPUs. This platform enhances the speed of research and development, from AI learning to performing inference with the AI implemented in the machinery.
The system is built on NVIDIA Jetson, an AI platform designed for edge devices and ideal for autonomous driving. It features a high-performance GPU that can process a variety of AI algorithms at high speeds. Kubota's agricultural machinery is equipped with the Jetson for industrial use. Its advantage lies in its durability and stable performance, as it can be used in harsh farming conditions such as drastic changes in weather and temperature and severe vibrations and impacts.
This industrial NVIDIA Jetson features Edge AI software, which is an essential technology for achieving automated driving. Edge AI has functionality to assess information that requires urgent action and make determinations such as stopping to avoid humans, animals, and other intrusions in its path during automated operations. It also minimizes the time lag between determining the situation and taking action.
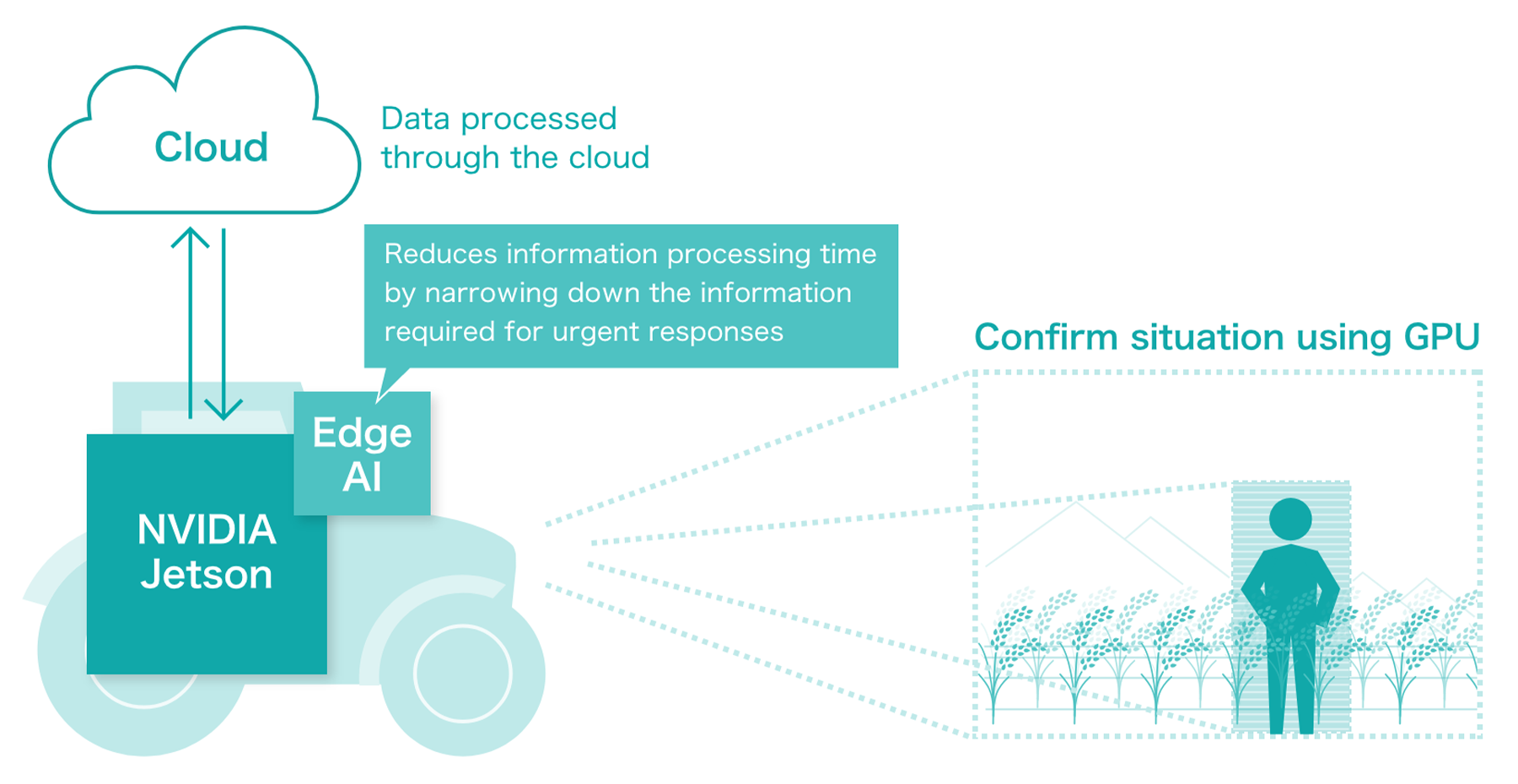
To train the AI in NVIDIA Jetson, Kubota has adopted the NVIDIA DGX system, which supports deep learning*2 software and is designed for GPUs. The data obtained by agricultural machinery with NVIDIA Jetson on board is inputted into the NVIDIA DGX computer, and this data is used as learning data to develop the AI. The completed AI is then implemented onto NVIDIA Jetson to perform inference with Edge. NVIDIA DGX and NVIDIA Jetson share the same GPU architecture, so AI developed with NVIDIA DGX can run on NVIDIA Jetson, enabling more efficient R&D.
- *2.Deep learning: A machine learning method using multi-layered artificial neural networks.
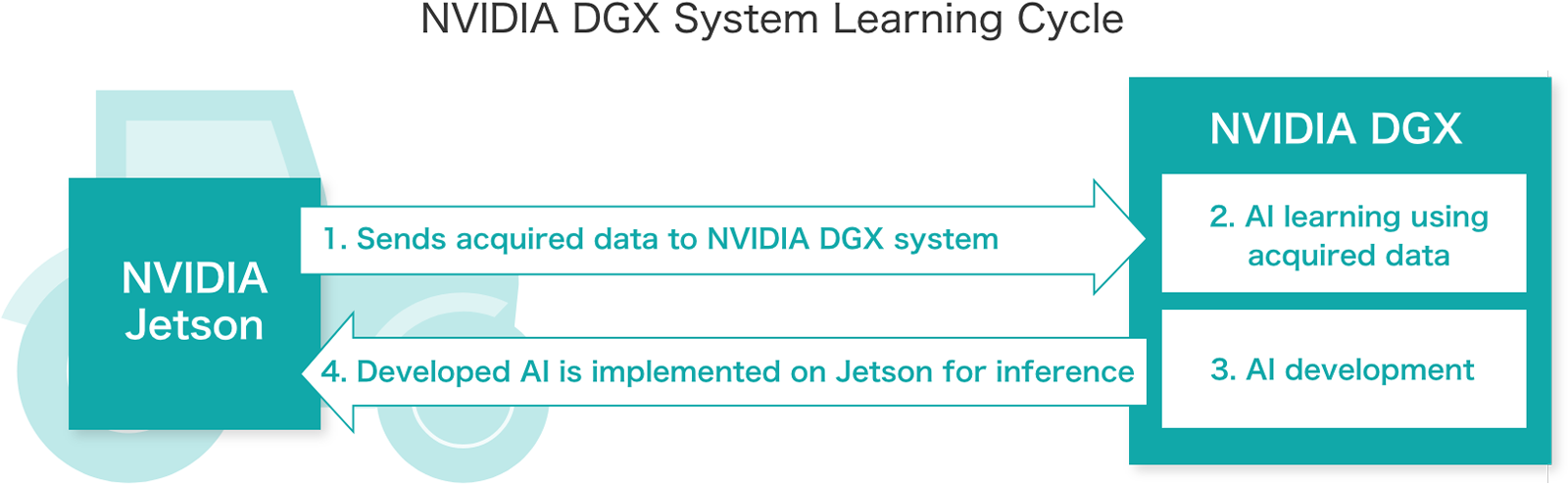
The NVIDIA end-to-end AI platform was considered to be the optimum choice for Kubota's vision of automated and unmanned agricultural machinery. Overseeing the strategic partnership with NVIDIA for this purpose was Kenichi Iwami, General Manager of Technology Innovation R&D Dept. II at the Technology Innovation Research and Development Unit in the Research and Development Headquarters. He talks about the challenges that Kubota must overcome and his hopes and expectations for the project.
Kubota’s Vision of Realizing “Completely Unmanned Operation of Agricultural Machinery”
The tractors, combine harvesters, and rice-transplanters for Step 2 in Kubota’s vision for automated and unmanned agricultural machinery, “automation and unmanned operation under monitoring by people,” have been released. What are some of the issues you face and the initiatives you are taking as you proceed from Step 2 to Step 3, “completely unmanned operation”?
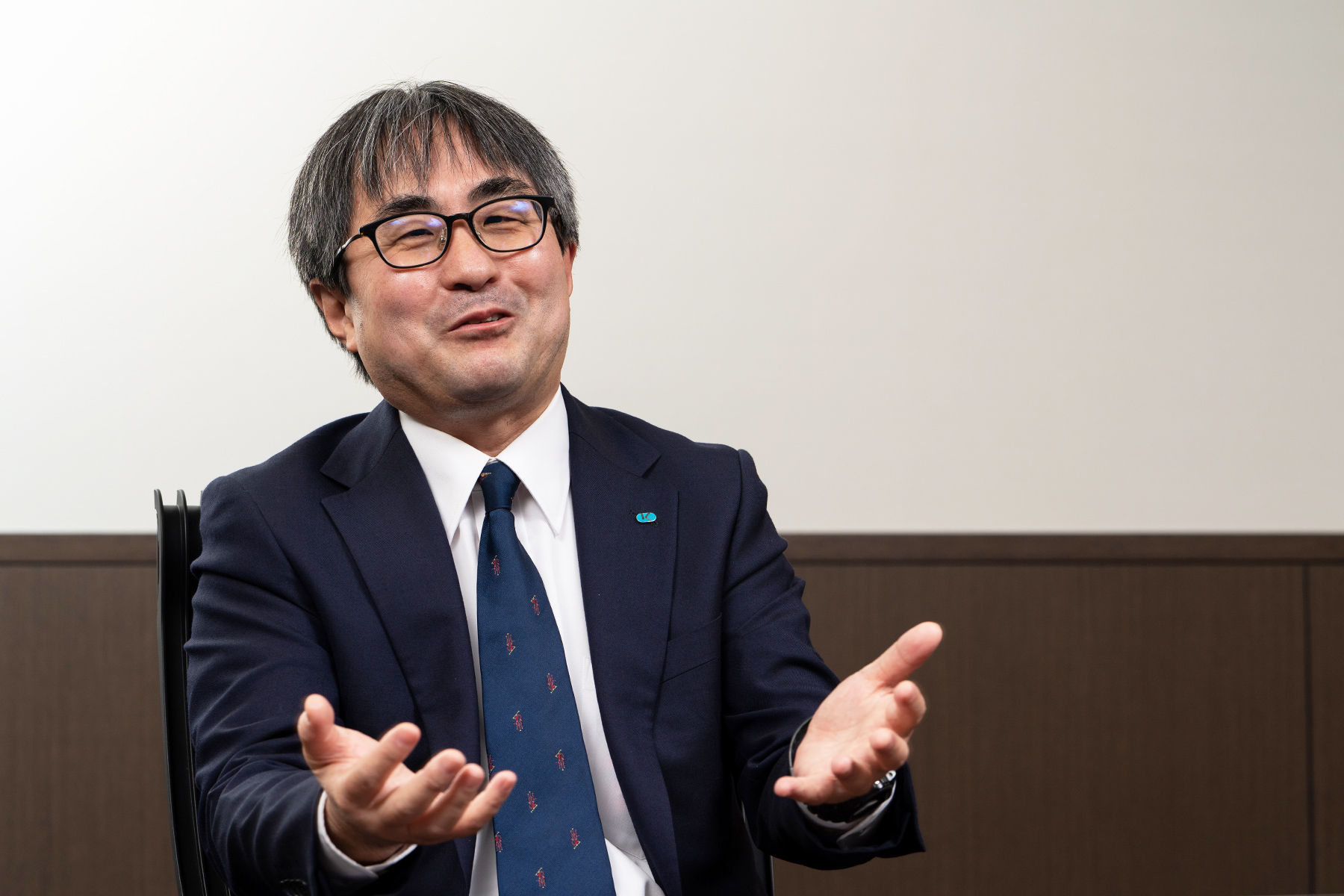
"What we have achieved in Step 2 is agricultural machinery that follows a predetermined route and performs predetermined farming tasks. In contrast, what we are aiming for in Step 3 is for the machinery itself to think and perform the optimal tasks. AI-enhanced agricultural machinery receives commands from people in remote locations, thinks with the skills and experience of an expert farmer, and determines what to do based on the conditions of the field*3 and crop growth. What this requires is AI with a brain and eyes like those of a human.”
- *3.Field: Areas of farmland on which crops are raised.
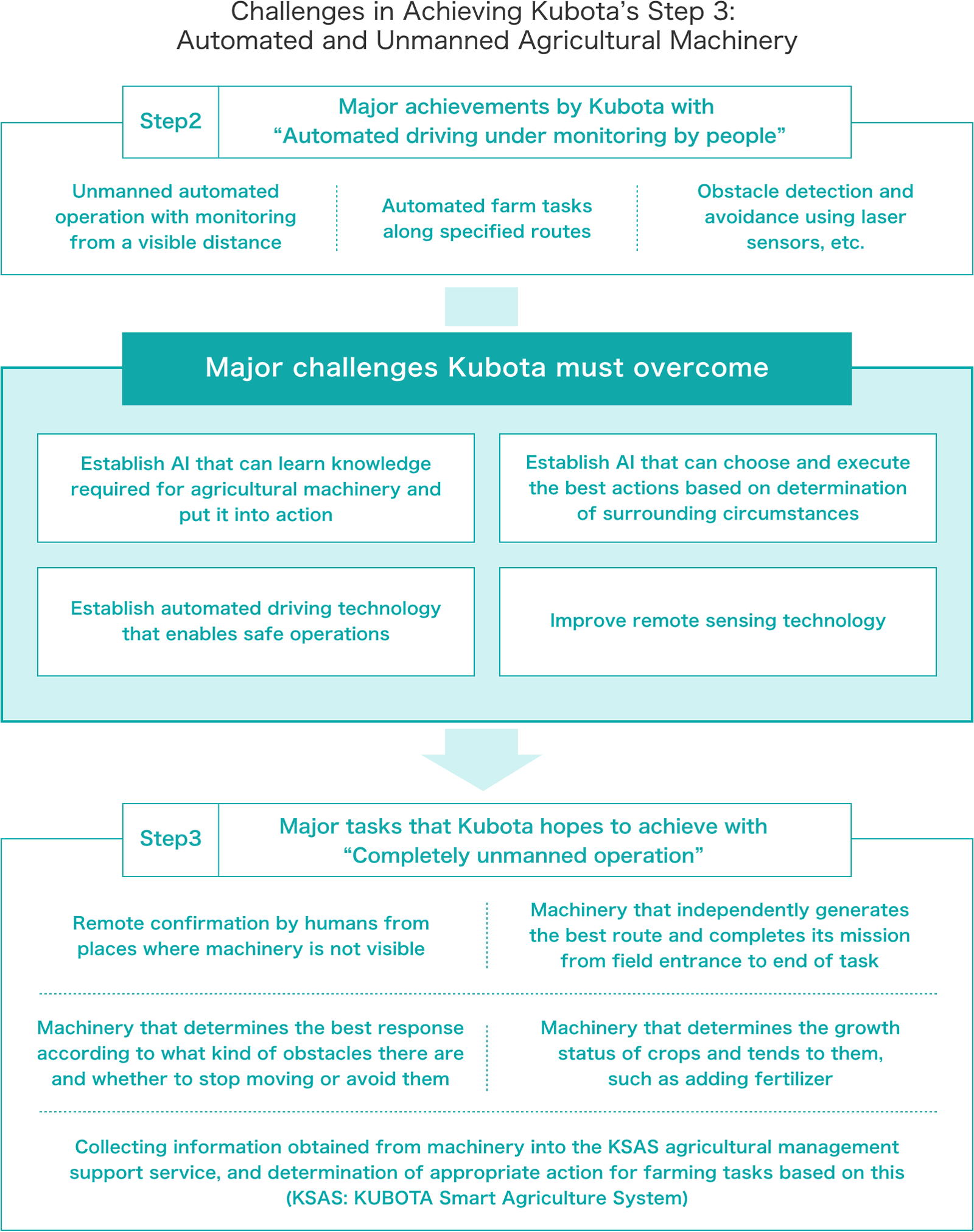
What are the keys points for developing AI with that kind of brain and eyes?
“There are three key points. The first is equipping the system with Edge AI that does processing with a controller built into the machinery, since the AI processing for automated driving demands high speed and dependability. The second is to have the system flexibly support the latest AI algorithms that are constantly evolving. And the third is to have it operate with stability even in a harsh farming environment. We began to think around 2015 that we needed an AI platform to address these three key points. After researching and verifying AI platforms provided by semiconductor manufactures in Japan and other countries, we found that the NVIDIA Jetson AI platform, with its high-performance GPU and reliability, offered outstanding performance in all three areas.”
The role of the eyes is given equal priority to the brain. How does this differ from Step 2 to Step 3?
“For completely unmanned agricultural machinery, the eyes play two roles. The first is recognition of the surroundings, and the second is recognition of the field. For the surroundings, we now use laser and sonar sensors to detect whether obstacles are present, but we cannot tell whether they are people, animals, weeds, or rocks. Recognizing the surroundings in Step 3 means determining whether the objects are people, animals, plants, or something else, and taking the most appropriate actions. From there, recognition of the field takes over the role of optimizing farming tasks by fine-tuning how the equipment operates according to soil conditions and crop growth. For example, after a typhoon has passed, an experienced farmer would harvest with a combine harvester based on which way the rice plants have fallen. We will make that possible.”
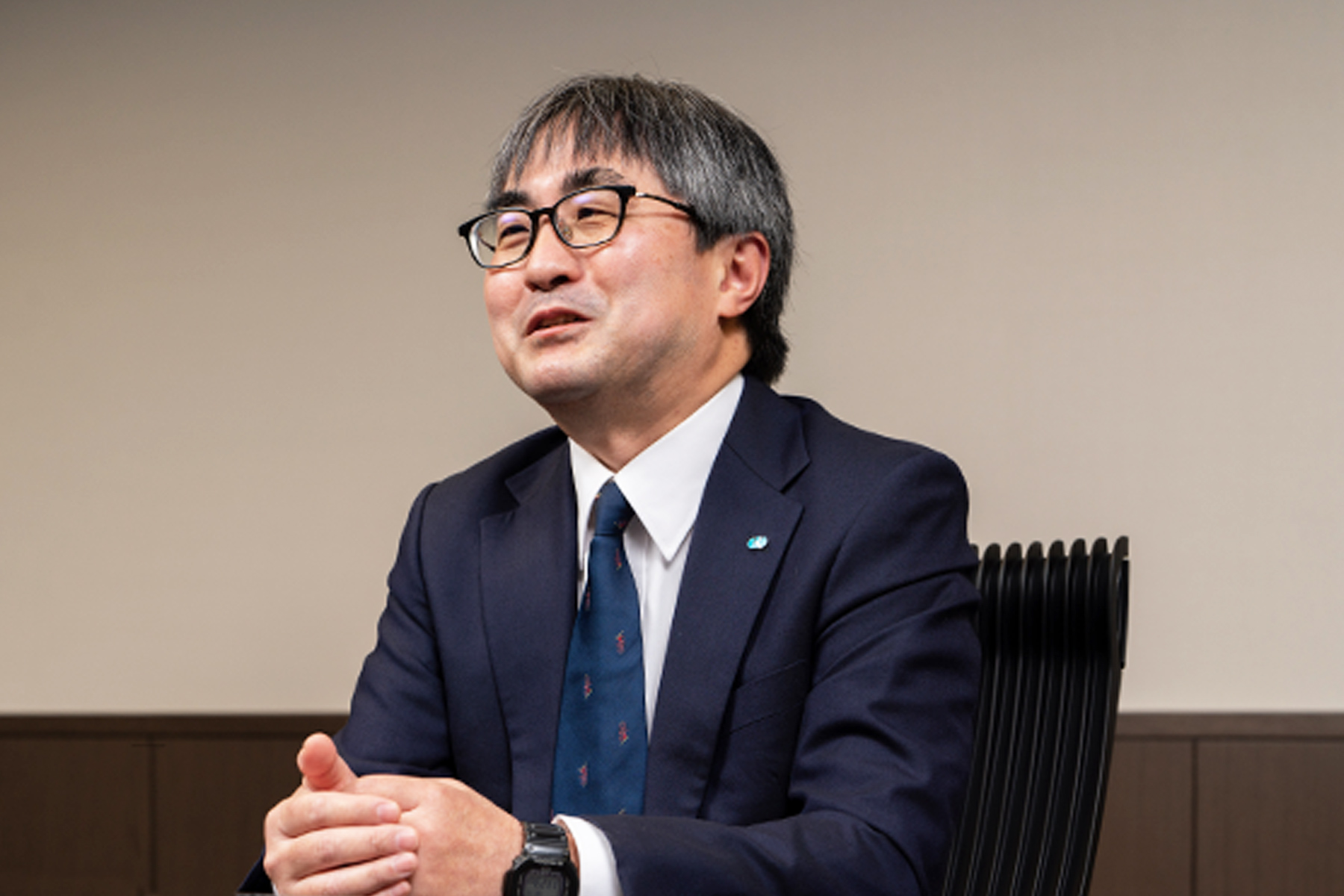
What initiatives will you take to achieve Step 3? And what is Kubota’s vision for the future of farming?
“At this time, we are installing Jetson on agricultural machinery to collect and gather various kinds of data, and using this data to train the AI on the NVIDIA DGX system. All of the issues involved in achieving Step 3 are challenging, so we will start by adding more difficult levels of tasks to each of the tractors, combine harvesters, and rice-transplanters that have achieved Step 2, and then release Version 2 and Version 3. In the process, we will overcome our challenges one by one toward realizing Step 3. The number of skilled farmers is decreasing, but even unskilled farmers will be able to work more efficiently if their machines can think of the optimum tasks on their own and respond flexibly to changes in circumstances. We would like to be the ones to make such a future of farming possible.”
When you hear the term “automated driving,” you may get the impression that the automobile industry is leading the way because there is so much information about it. However, Mr. Iwami’s words have reminded us that the agricultural industry is also at the forefront of automated driving, since its machinery does farm work automatically to help save labor and improve efficiency. A number of other challenges must be overcome before we have agricultural machinery that can think for itself and carry out its missions after receiving commands from humans. As Kubota works to achieve Step 3, we are looking forward to seeing how it will continue to develop machinery with added value.