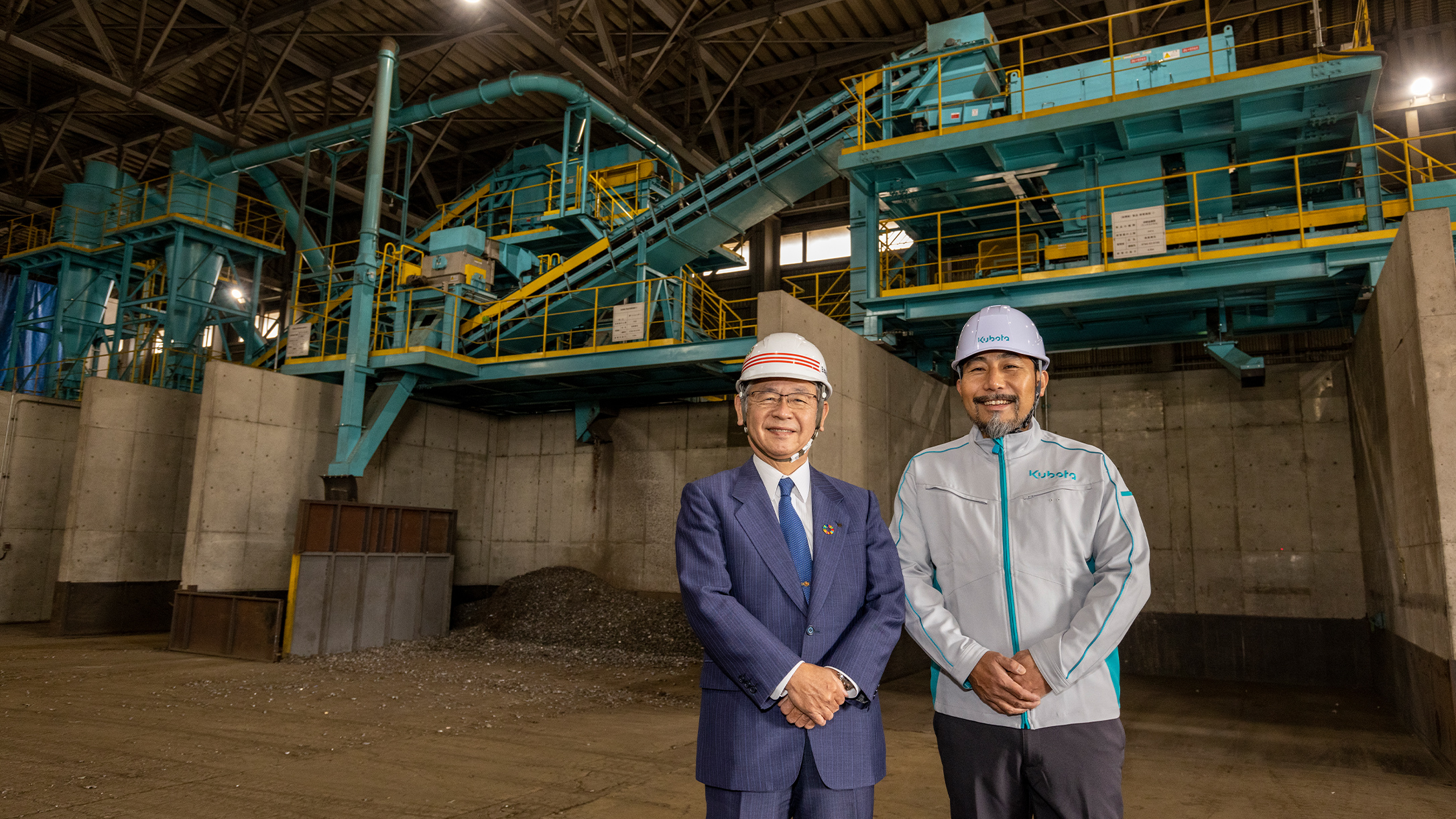
Environmental pollution caused by increasing amounts of plastic waste in the oceans is becoming a more serious problem throughout the world. In Japan, the Act on the Promotion of Sorted Collection and Recycling of Containers and Packaging was passed in April 2022, another sign that concern toward recycling issues is increasing both in Japan and abroad.
As part of Kubota's aim to be an “Essentials Innovator for Supporting Life,” committed to a prosperous society and the cycle of nature, the company is putting efforts into the core of its recycling operations: the development of shredders and its Plant Solutions Business.
For this article, we visited a new recycling plant where Kubota's shredders are at work. What we saw was that these high-performance shredders are more than just tools for shredding waste; they are machines that can "produce" useful metals and an invaluable tool for realizing a recycling-based society.
A Plant that Recycles Items from Train Cars to Small Home Appliances
The district of Fushiki in Takaoka City, Toyama Prefecture, once prospered as a key trading location for the Kitamae-bune (northern-bound merchant ships) from the 1600s to the 1800s.
This is the location of the head office and plant of Nihon Sougou Recycle Co., Ltd., an advanced recycling business that goes beyond expectations. KUBOTA Environmental Engineering Corporation oversaw the plant's design, including the shredder.
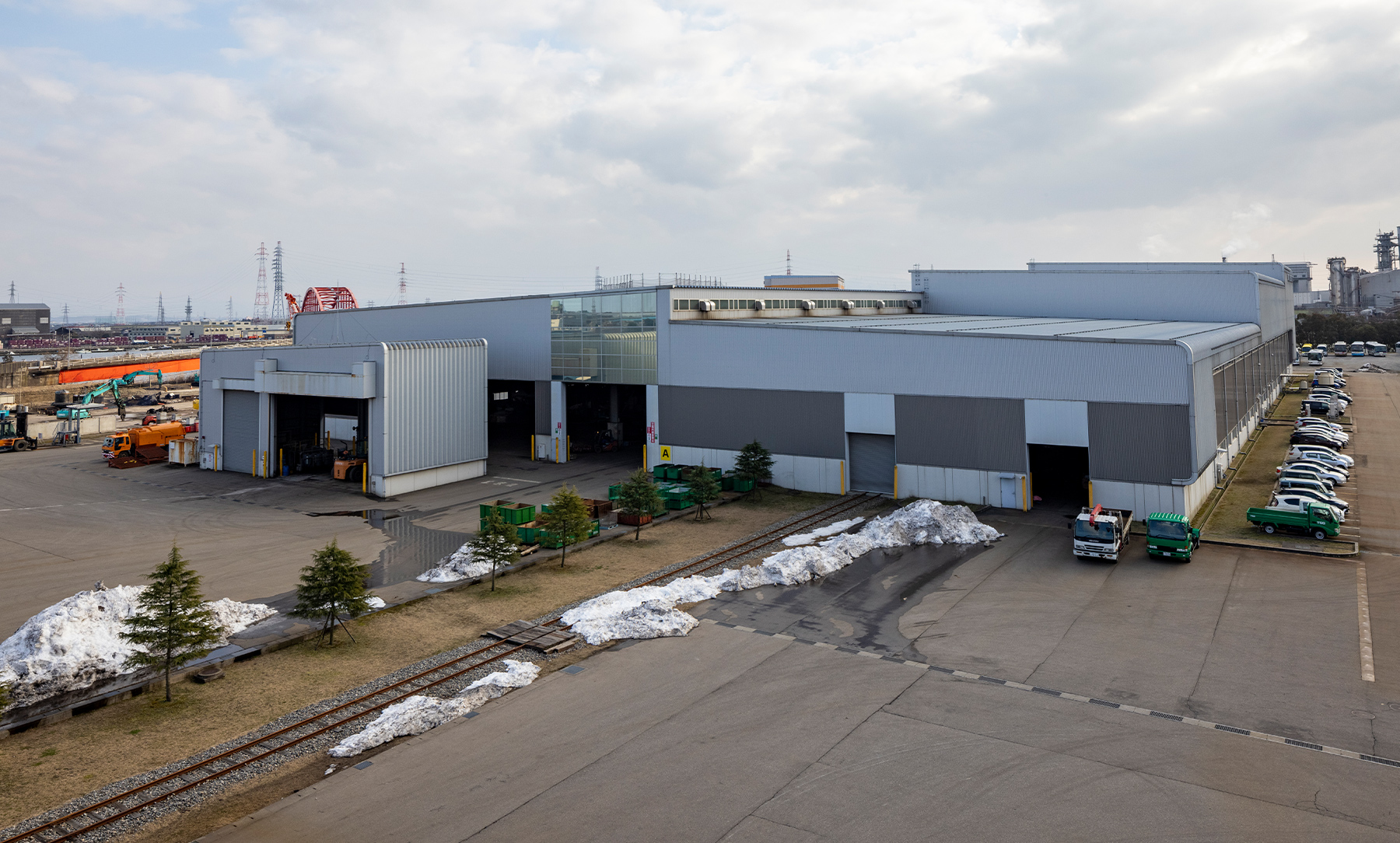
The company was established in 2009 as the fourth group company of Toyotomi Sangyo Co., Ltd., a comprehensive recycling firm with a history of more than half a century, and its plant began operations in 2012. It was initially founded to recycle large vehicles such as trains and buses, but soon it began taking in small home appliances, electronics, motors, and machine switchboards. It is now involved in recycling not only iron, aluminum, and copper, but also the recovery of rare metals from “urban mines,” many of which have been shipped overseas.
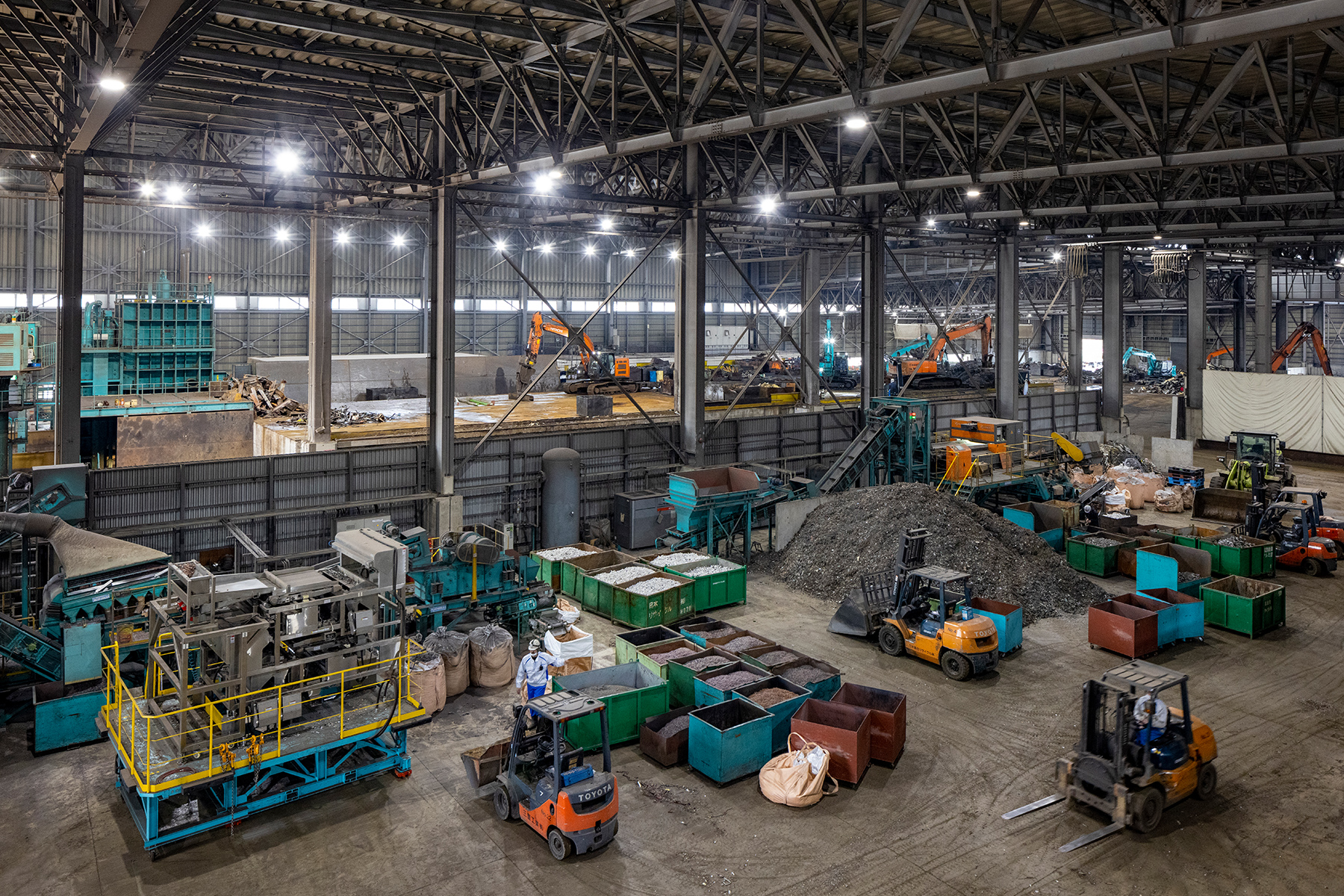
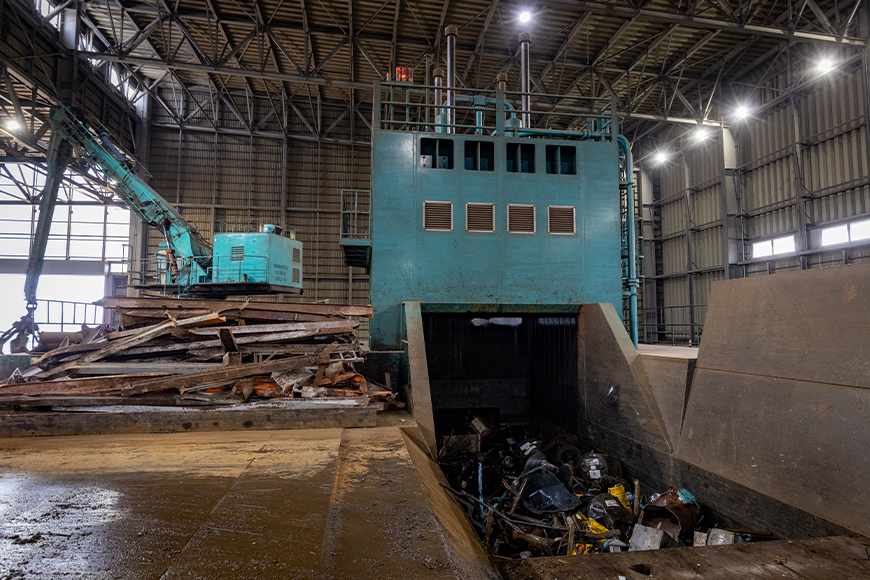
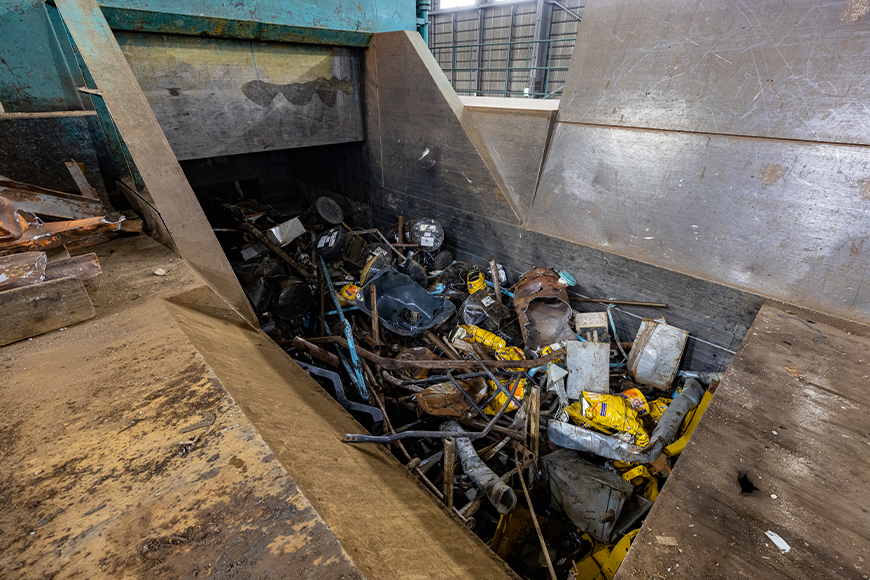
This large press shearing machine applies pressure all at once from the front, back, and sides, and is large enough to hold a full-sized train car. This revolutionary system uses Kubota's exclusive technologies. No trains were being handled on the day of our visit, but the sight of thick metal products being squeezed together and sheared with large blades was quite impressive when seen up close.
From Small Home Appliances Come Valuable Metals
During this visit, we were mainly shown the process for recycling home appliances and train cars dismantled into smaller pieces. With the replacement of the vertical shredder in August 2019, all recycle plant equipment that handles shredding processes had been upgraded.
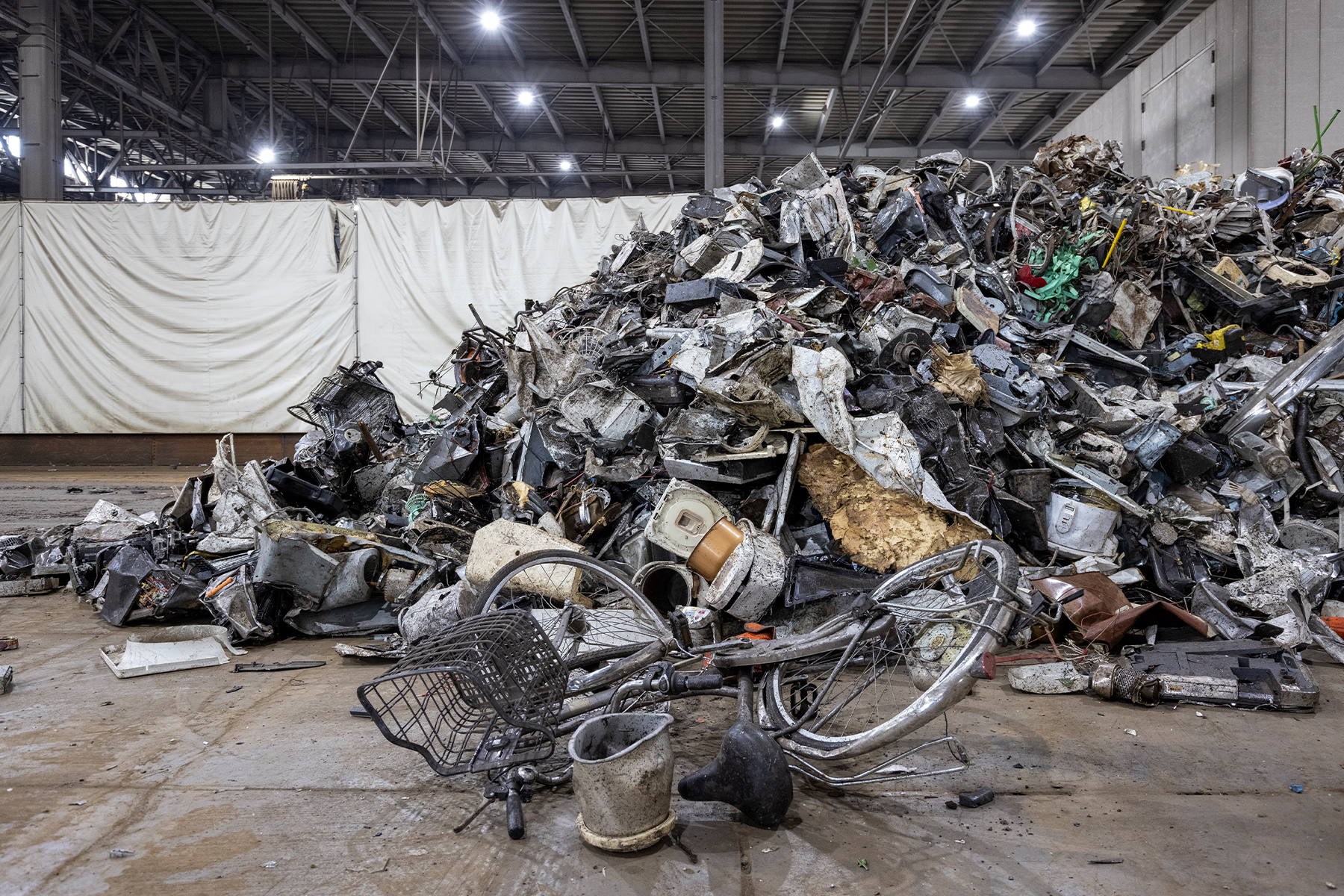
To prevent noise, vibration, and scattering of fine dust, shredders are built inside nested structures, with the machine placed inside an additional small building built inside the plant. First, piles of resources are continuously fed by heavy machinery into the hopper at the conveyor belt entry point in the front of the structure. This belt transports the items to the shredder inside.
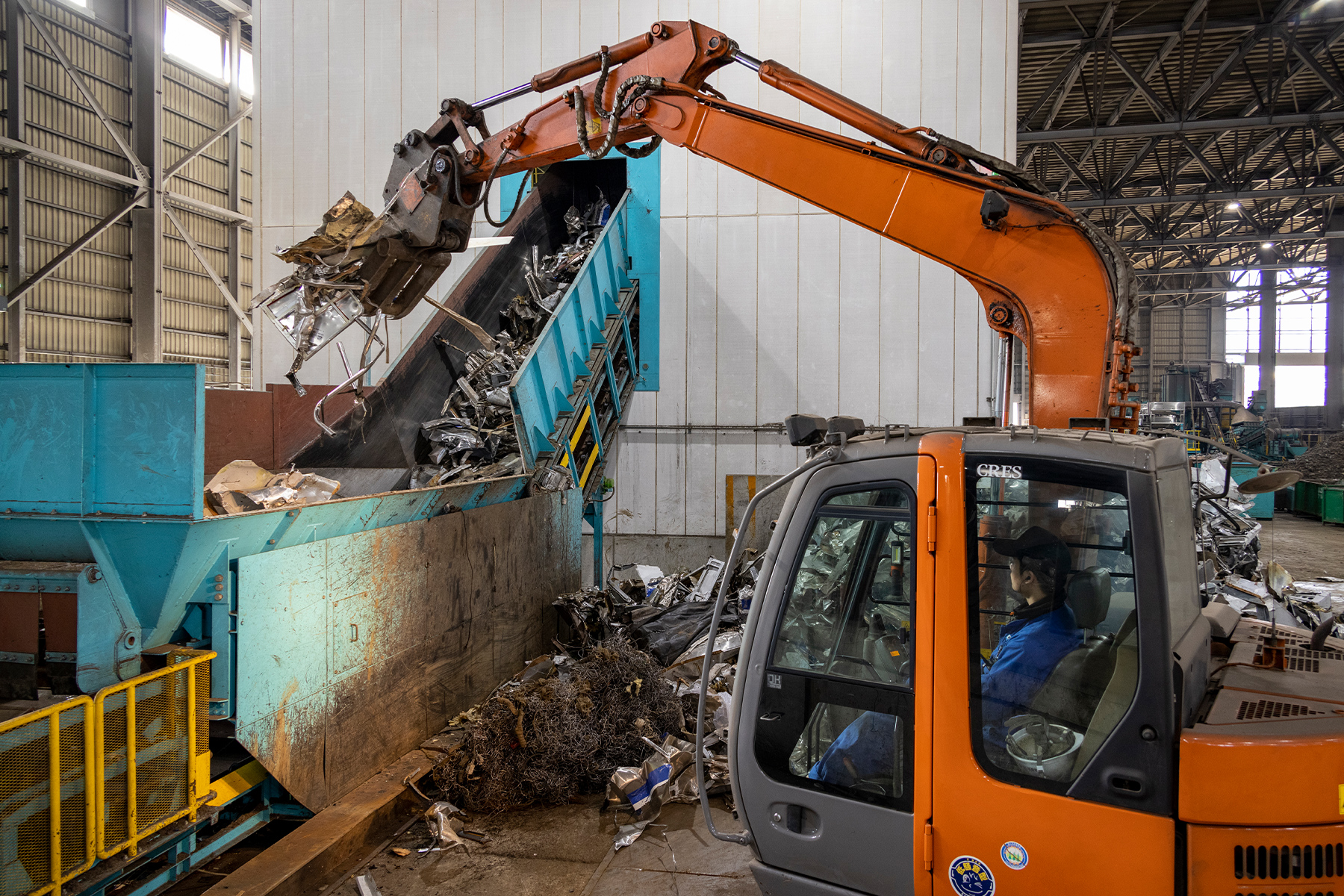
When we step inside the building, the noise gets even louder – so loud that we can hardly hear ourselves talking. A Kubota vertical shredder is used in this area. It features a breaker that rotates at high speed for coarse shredding and a grinder for fine shredding (compression, tearing, rubbing). This means everything from soft tatami mats and plastics to hard metals and concrete can be shredded all at once.
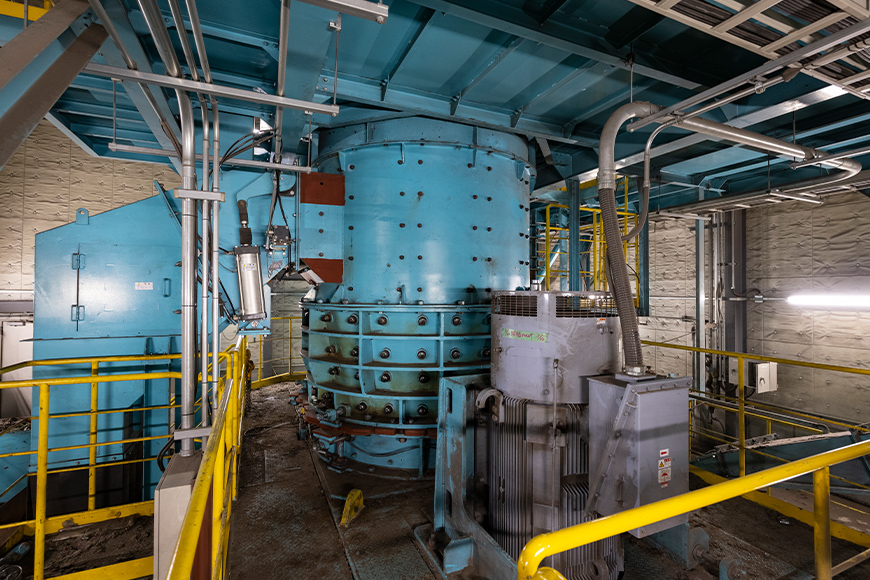
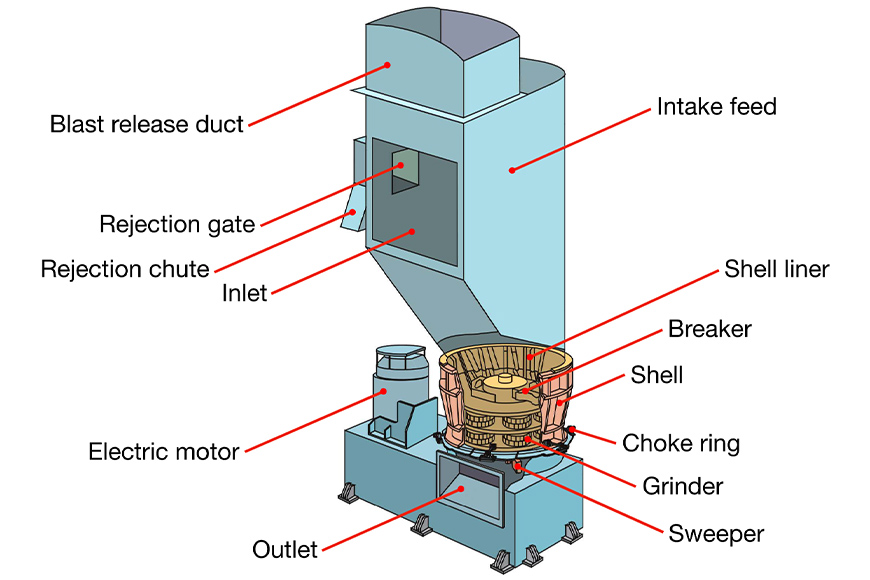
This is an exterior view of the shredder installed inside the factory's structure. The breaker and grinder, the main components of the shredder, are inside the cylindrical-shaped unit. The combination of the breaker and grinder enables fine and highly consistent grinding, improving accuracy of sorting in later processes and enhancing the value of the resources.
The shredded resources are then sent to the magnetic separator.
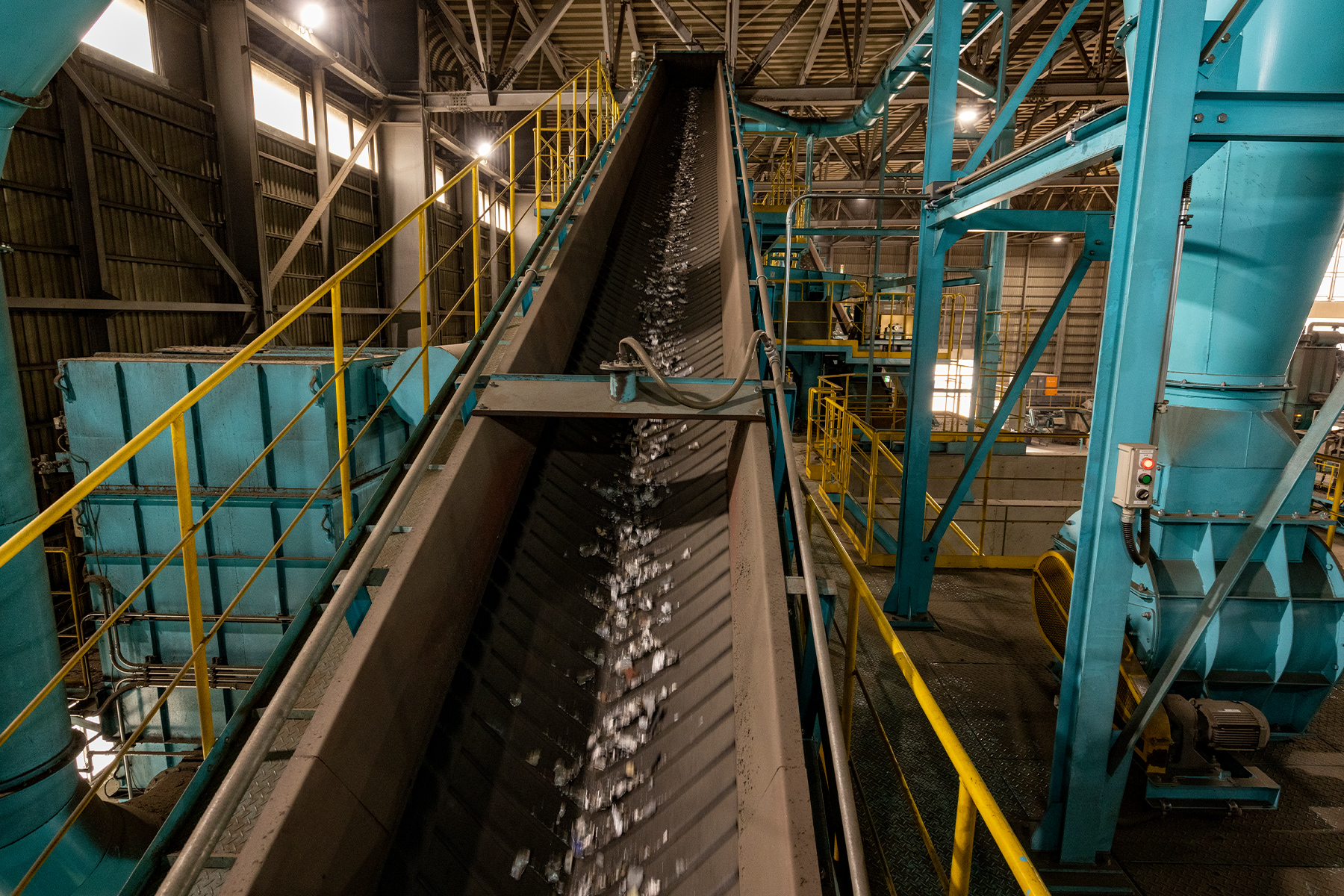
The magnetic separator sorts ferrous and nonferrous metals. Then the nonferrous metals are passed through a trommel. Then they are sorted into coarse and fine materials, and each is then passed through various sorting machines to separate them into metals such as stainless steel, aluminum, brass, and copper.
After passing through each process, the separated metals are finally dropped into small, walled-off room-like spaces called "yards" for storage. One feature of this recycling plant is that it has a two-level structure with equipment placed above the yard separated by high reinforced concrete walls. The aisle was narrow in the past because the recycling plant was pushed out in front but is has been widened thanks to the vertical use of the space, allowing plenty of room for vehicles to enter.
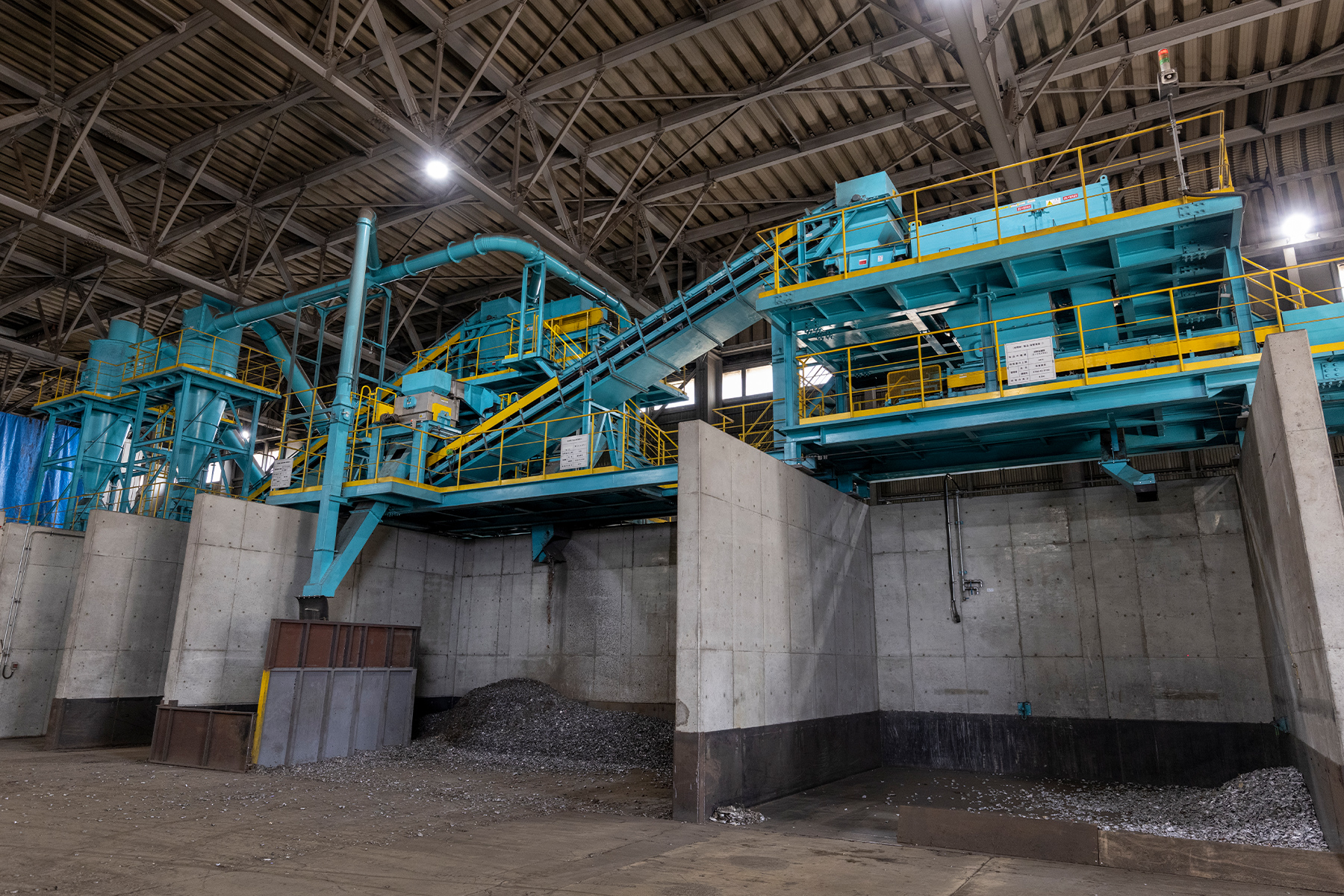
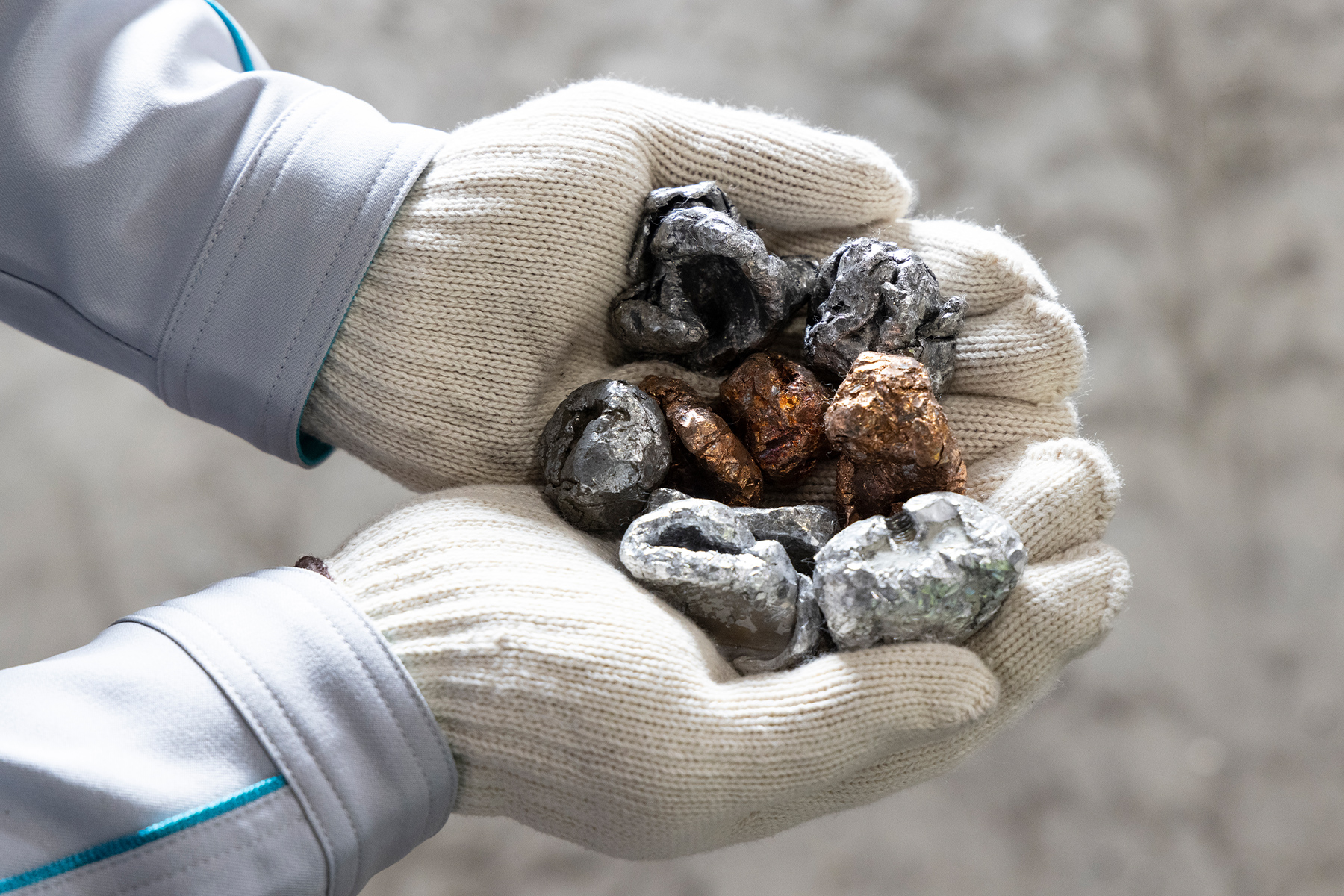
Plant Design Influences Productivity Along with Shredder Performance
After being given a tour of the resource recycling processes, we asked Mr. Yasushi Takakura, the President of Nihon Sougou Recycle Co., Ltd., about how they came to use Kubota shredders.
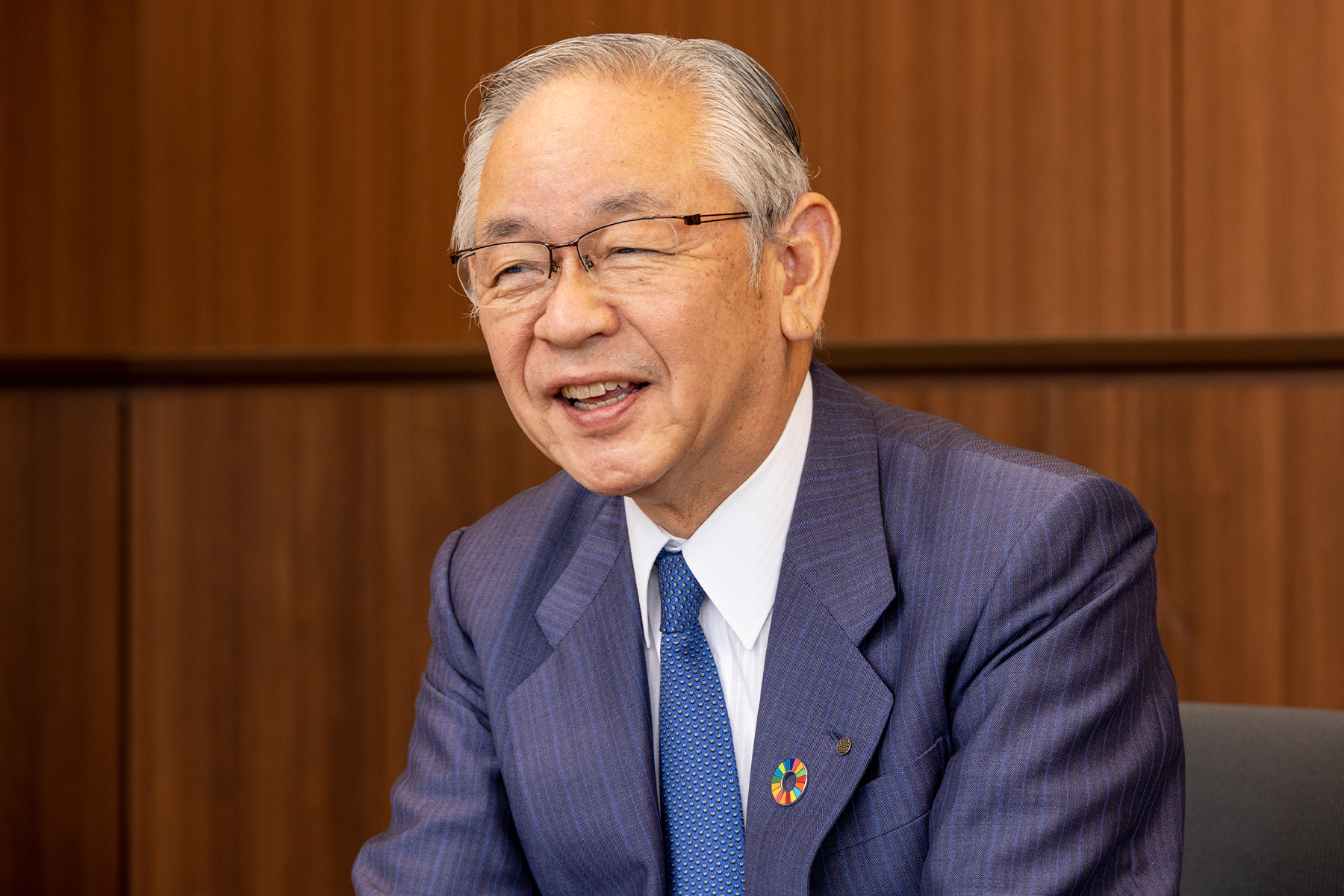
Takakura says that when the plant was first built, they installed a shredder from another manufacturer. However, it broke down often and the plant had to be shut down several times, so he decided to replace it eight years later. He says that the company appreciated Kubota's solution, which included not only the shredder but also consideration of which other equipment to choose and how to best arrange the machines to maximize the performance of the shredder. They ultimately decided not only to start using a Kubota shredder but also to ask Kubota to assist with the design of the plant.
“The area that improved most was our yield. Now we can efficiently collect iron, aluminum, copper, stainless steel, and even rare metals. And we have a better balance with other equipment such as our dust collector, so I think we are doing a good job of collecting the shredded materials. Our recovery rate has improved just as we had expected.”
In addition to their fine and uniform shredding, the fact that employees can adjust the particle size and easily change parts was another benefit of Kubota shredders. This enables recycle plants to operate with shorter periods of downtime and drastically cut maintenance and running costs. Plus, the higher partition design for the yard diving walls has been a success. Takakura adds, “The optical sorter we added in 2021 fits right into the yard, so now we can do even more precise sorting.”
KUBOTA Environmental Engineering Corporation's Daisuke Hamada, who was involved in the recycling plant's overall design during the renovation of the shredder line, told us, “Replacing a shredder that would normally last 20 years after only eight years was a very wise decision. That's why when I took over the planning, I felt a certain sense of pressure to create a recycling plant that would never stop operating.”
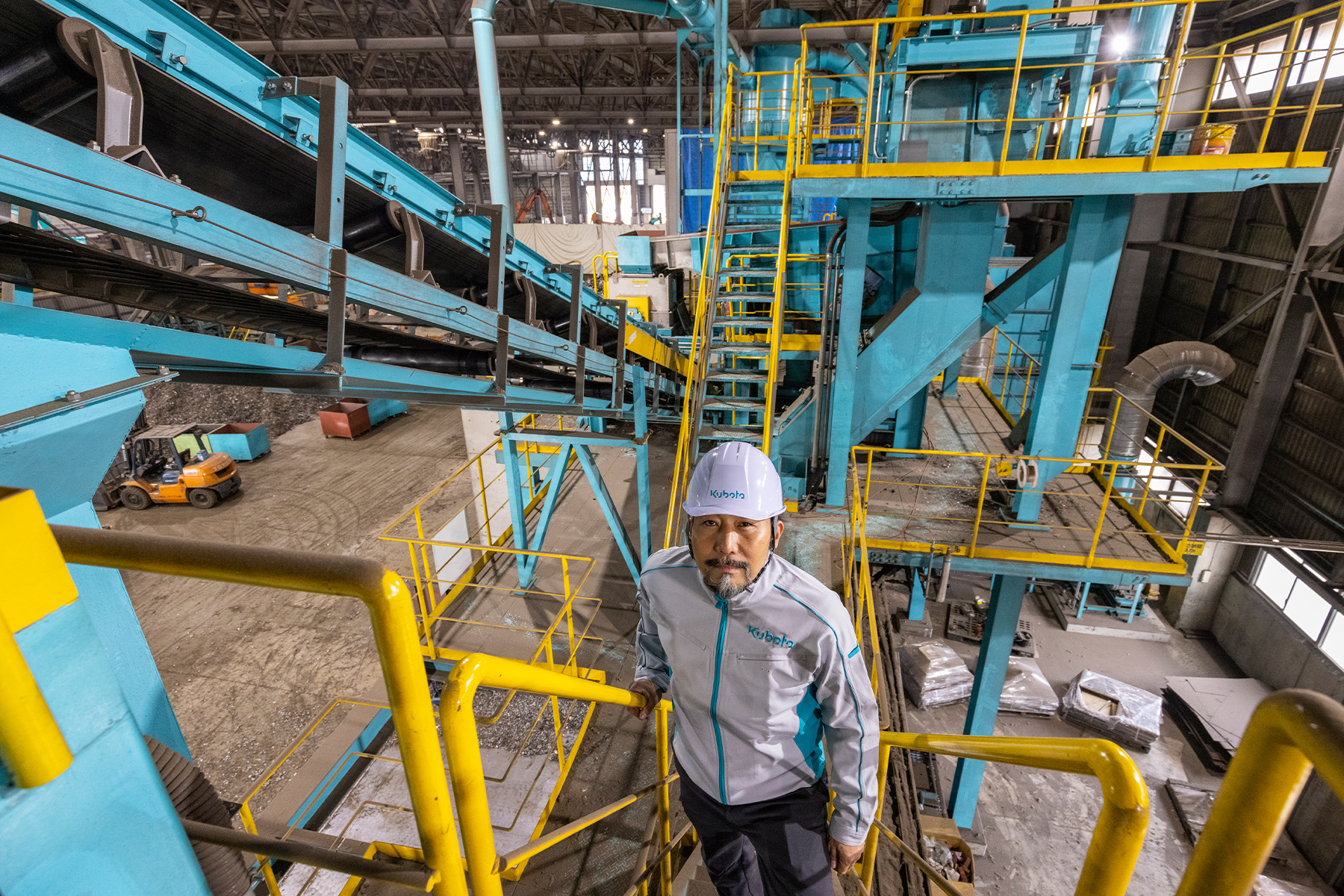
When Hamada first visited the headquarters in Toyama, he could sense that tremendous care was being taken about dust collection throughout the plant. He was also impressed by a comment from the chairman who founded the plant: “Recycling plants of the future need to be places where customers can visit wearing full suits and shoes.” Hamada says, “The yard is a place where they show customers all products, including steel and aluminum. In that sense, I think their yards are now spaces where things are easy to see.”
Takakura concluded the interview with this statement:
“Kubota's shredders have become what they are today through repeated improvements and refinements over a long time. I believe that is what having a history means. I could also sense Kubota's essence in the fact that they are by our side all the way. I hope we can continue to exchange ideas and work on new initiatives.”
Aiming for Technological Development that Contributes to Material Recycling
Finally, we talked with Wataru Sone, Office Manager of Resource Circulation Business Planning and Sales Department at Kubota. Sone has been involved with environment-related businesses for nearly 30 years, and he says that he has sensed changes in trends over times from “waste treatment” to “resource recovery” and furthermore from “recovery” to “recycling” and “circulation”.
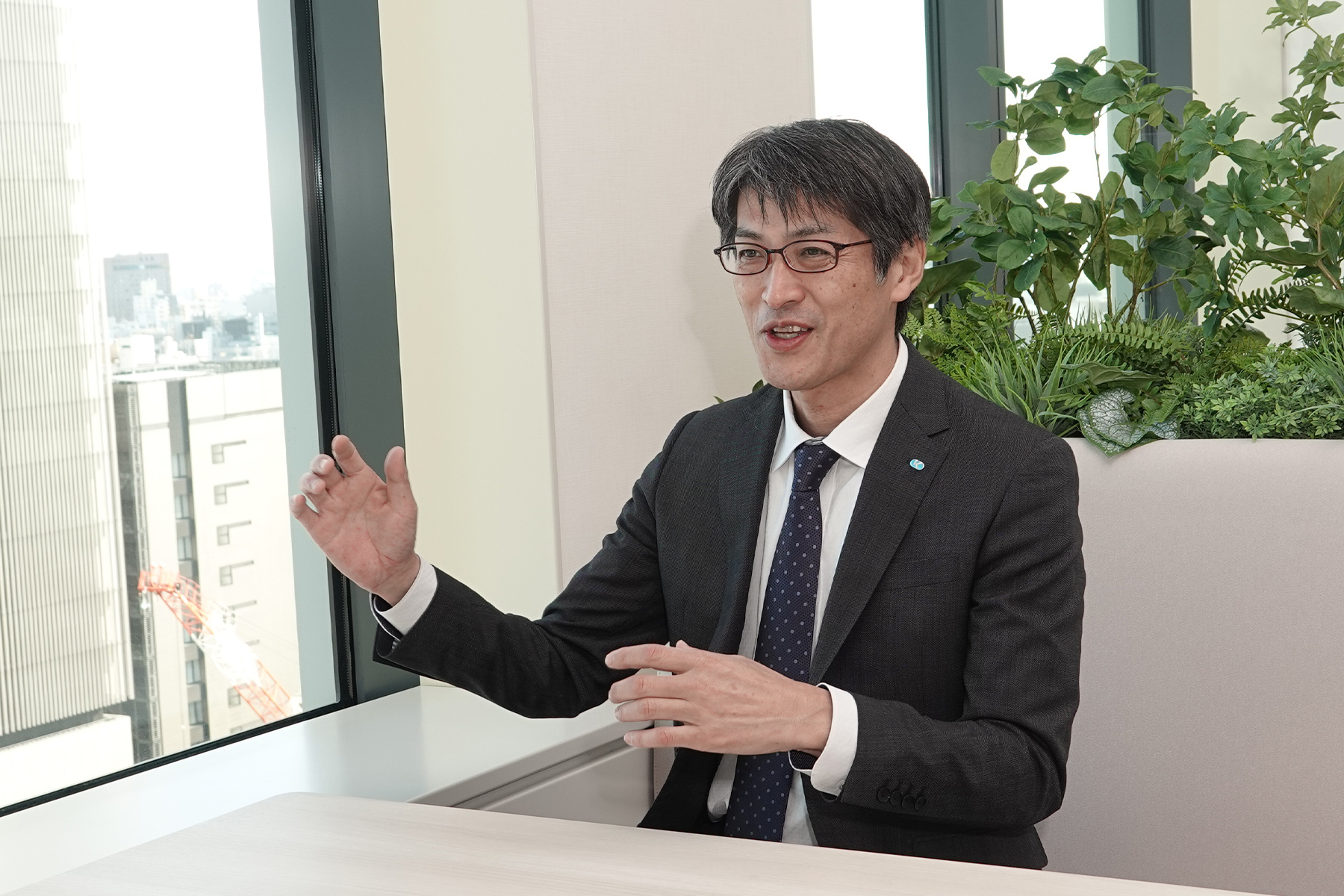
When we asked Sone about where Kubota's shredders show their advantages, he gave the following reply.
“Given the heightened awareness toward recycling, the popularization of the term 'carbon neutral,' and the emergence of the microplastics issue, we have worked to respond to a variety of changes in social conditions by refining and evolving our technologies. I believe that having made these small improvements repeatedly over a long period of time has led to stability and reassurance in all aspects of our business, from manufacturing to sales and maintenance.”
According to Sone, shredders today are more than just tools for shredding waste products. They can also be said to play an important role in the production of useful metals. Going back in history, shredders were originally machines created to shred huge rocks at mines. But their purpose of use has changed with new trends in society, and each time they have continued to evolve, so that now they are used as machines for separating useful and valuable minerals.
In the past, as with plastics, there were many cases of materials being burned for use as fuel or put through “cascade recycling” in which the original products are recycled into new products or materials of degraded quality, says Sone.
“However, the trend of 'horizontal recycling,' in which used products are converted into resources to create the same types of products again, will become mainstream. This plant will be the site where such resources are generated. Only when such a complete recycling of each material is achieved can we call this a true recycling-based society.”
As a company engaged in environmental businesses, Kubota promotes advancement of recycling by further refining its sorting technologies, focusing on its shredders. With this strong conviction, Kubota contributes to the realization of the circular economy.