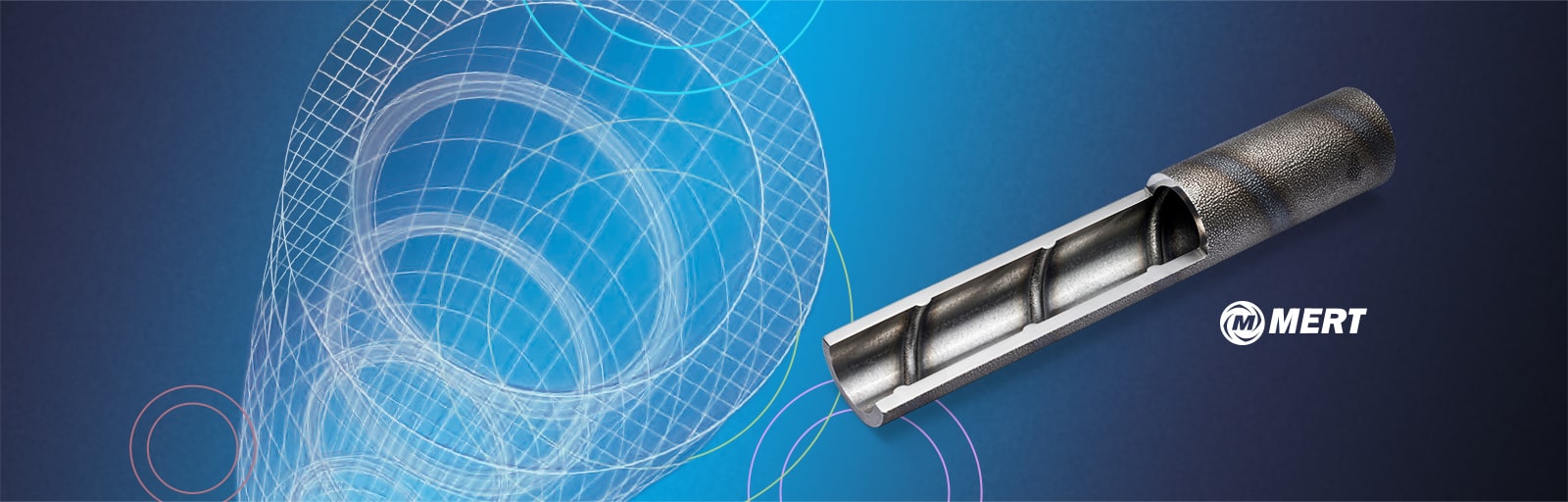
MERT
Mixing Fluid Gas inside the Tube Increases the Operation Efficiency of Thermal Cracking Furnaces and Extends Tube Life
Ethylene and propylene, the raw materials of petrochemical products, are obtained through cracking hydrocarbon feeds such as ethane or naphtha in cracking tubes in thermal cracking furnaces, using steam dilution.
Kubota's MERT (Mixing Element Radiant Tube) has helical ribs on the cracking tube's inside surface called "mixing elements" which mix the fluid gas inside to promote efficient heating and realize a uniform distribution of the fluid gas temperature. The benefits for users include reduced coking (carbon deposition caused by free radical carbons) with resulting increases in heating furnace utilization rate and production, lower energy consumption, and extended tube life due to lower tube temperatures.
Concept
MERT is a centrifugally cast cracking tube with helical mixing elements on the tube's inner surface, which, by stirring and mixing the feed gas inside, improves heat transfer and realizes more uniform internal fluid gas temperature distribution to improve cracking efficiency.
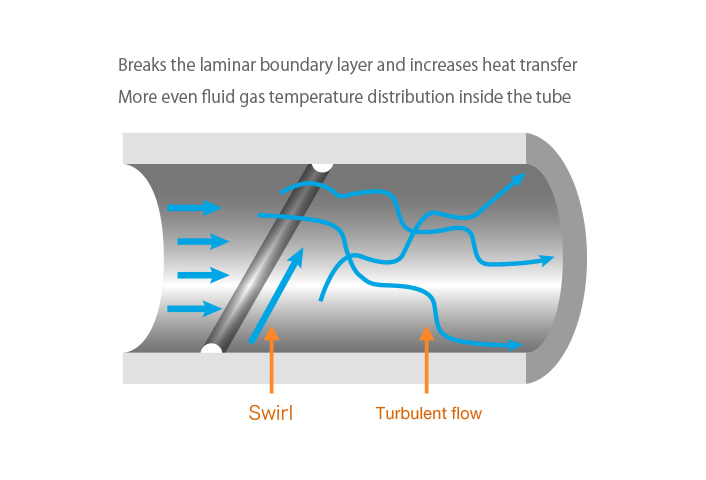
The stirring and mixing of fluid gases inside the cracking tube by the mixing elements break the laminar boundary layer on the tube's inside surface, which has very high heat transfer resistance. This facilitates heat transfer in the tube, resulting in lower tube outside surface temperatures and reduced coking (carbon deposition caused by free radical carbons) on the tube's inside surface, which extends intervals between decoking operations (removal of carbon deposition) and increases the utilization rate of thermal cracking furnaces.
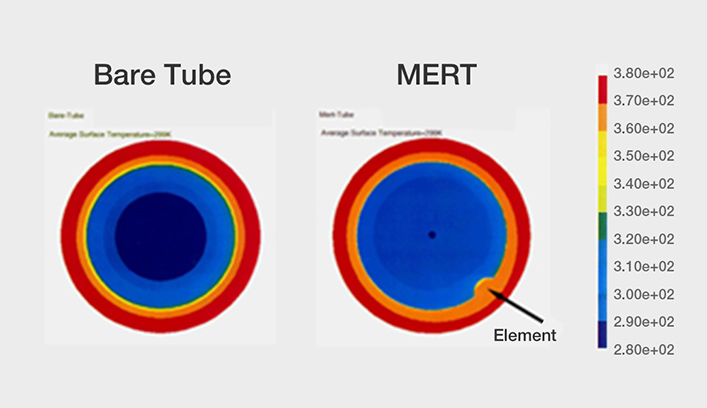
Since a cracking tube is heated in a thermal cracking furnace through radiation heat transfer onto the outside surface of tubes, gas temperatures rise high near the surface while temperatures remain low around the tube core, causing temperature gaps inside the tube. Where gas temperatures are too high, over-cracking occurs, causing the target products such as ethylene and propylene to decompose further and disappear. Because stirring by the mixing elements can flatten the fluid gas temperature distribution inside the tube and thus control over-cracking (allowing thermal cracking to occur evenly), larger ethylene and propylene yields can be expected.
MERT controls both catalytic and pyrolytic coking; it can effectively control coke formation in both naphtha cracking and gas cracking.
MERT Element Design Variations
MERT has continued to evolve since it was launched in 1996. We can propose an optimal design for particular thermal cracking furnace types and to meet individual requirements from the three different mixing element designs: MERT, Slit-MERT, and X-MERT.
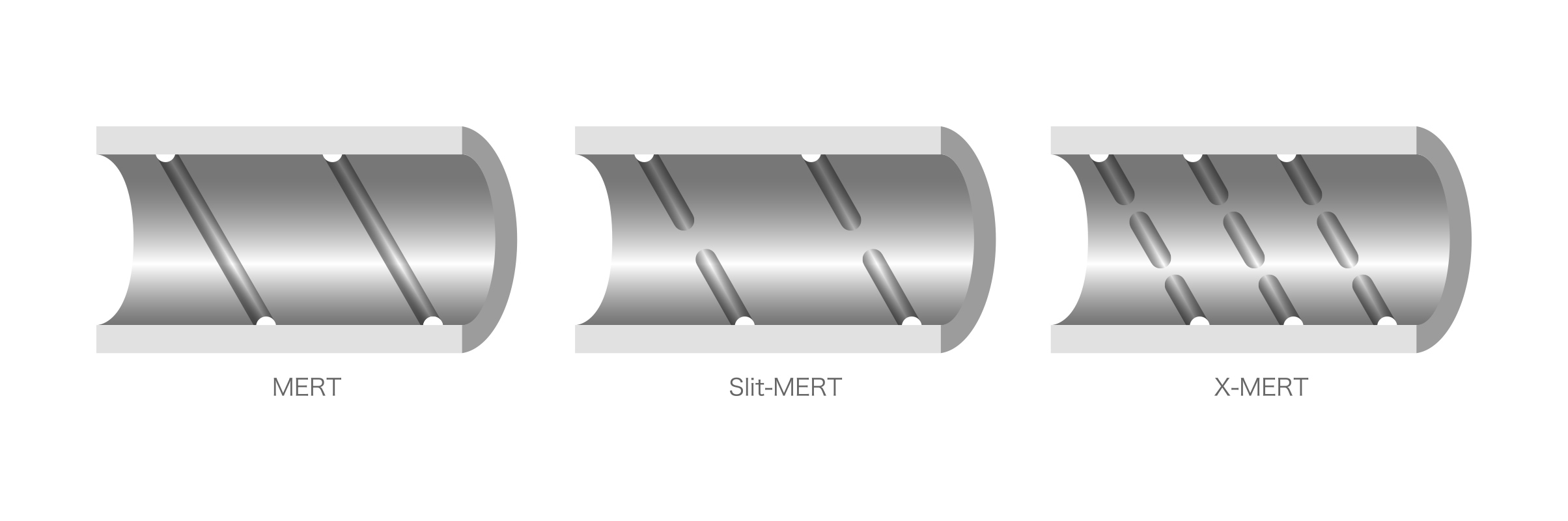
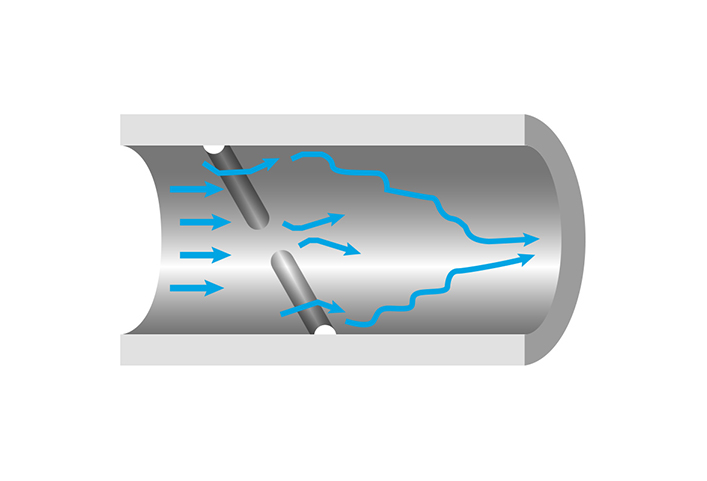
Slit-MERT can reduce pressure drop by 20% compared to MERT while maintaining high heat transfer performance. This element design is ideal for thermal cracking furnaces designed for small pressure drops, or where you wish to extend MERT-applicable tube length in a cracking coil.
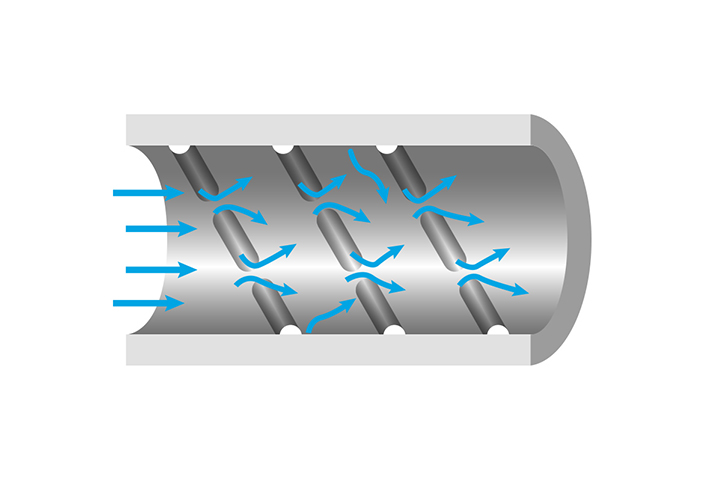
X-MERT was launched in 2007 as an improved version of Slit-MERT. Compared to Slit-MERT, it is possible to reduce the pressure drop by an additional 10%. X-MERT is applicable to wider furnace types and extends MERT-applicable tube length in a cracking coil without the limitation of pressure drop.
We can design mixing elements that are ideal for your cracking furnace type or furnace operation conditions to maximize operation efficiency.
Heat Transfer Characteristics Comparison between X-MERT and Slit-MERT by Thermo-fluid Analysis Using CFD (Computational Fluid Dynamics)
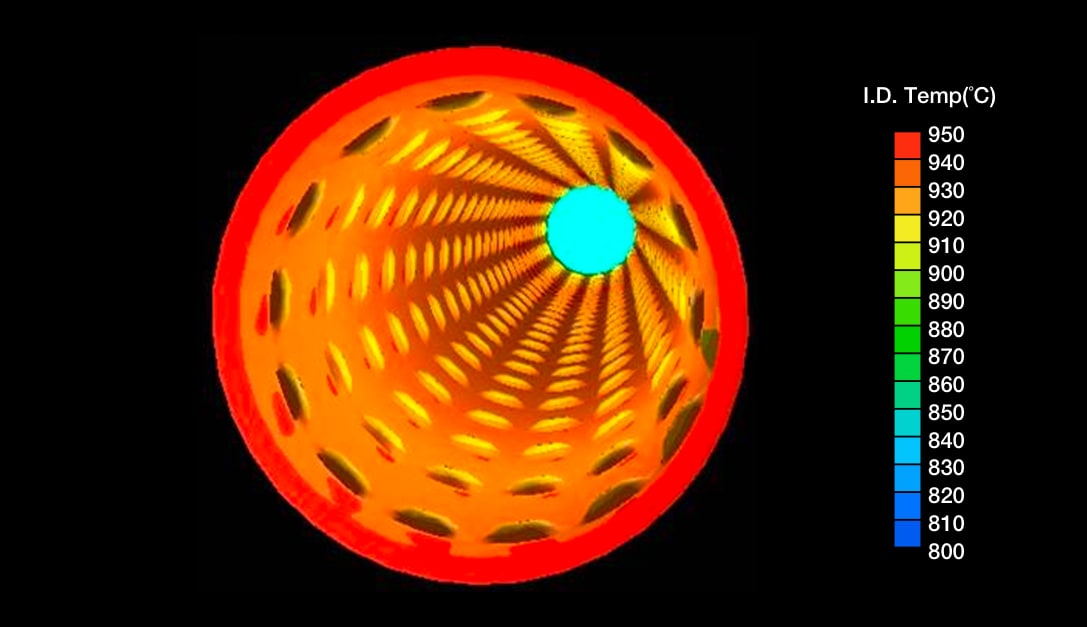
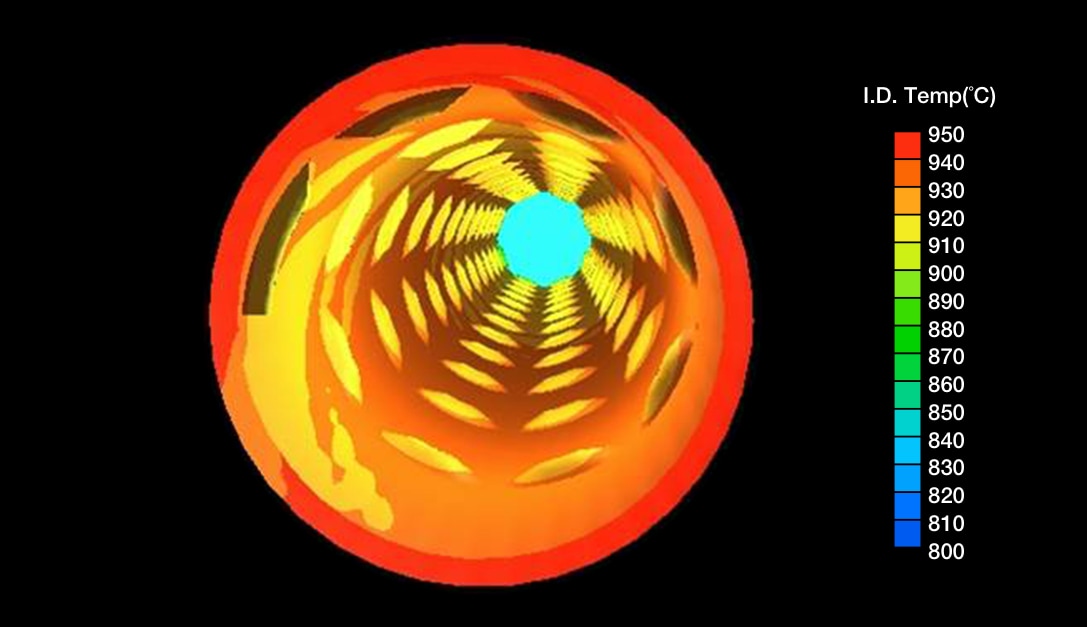
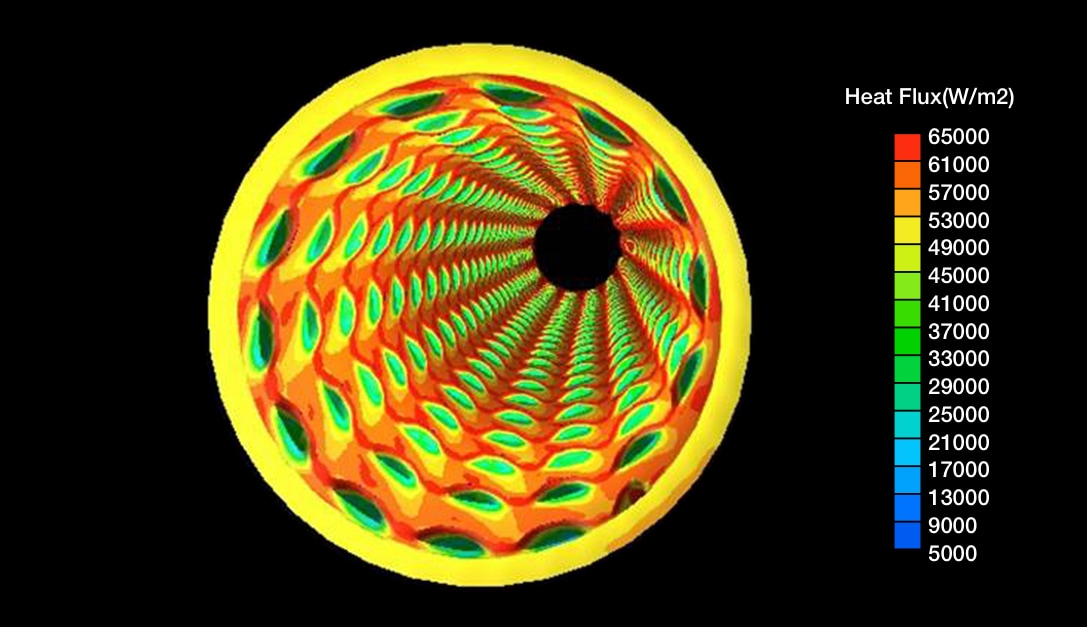
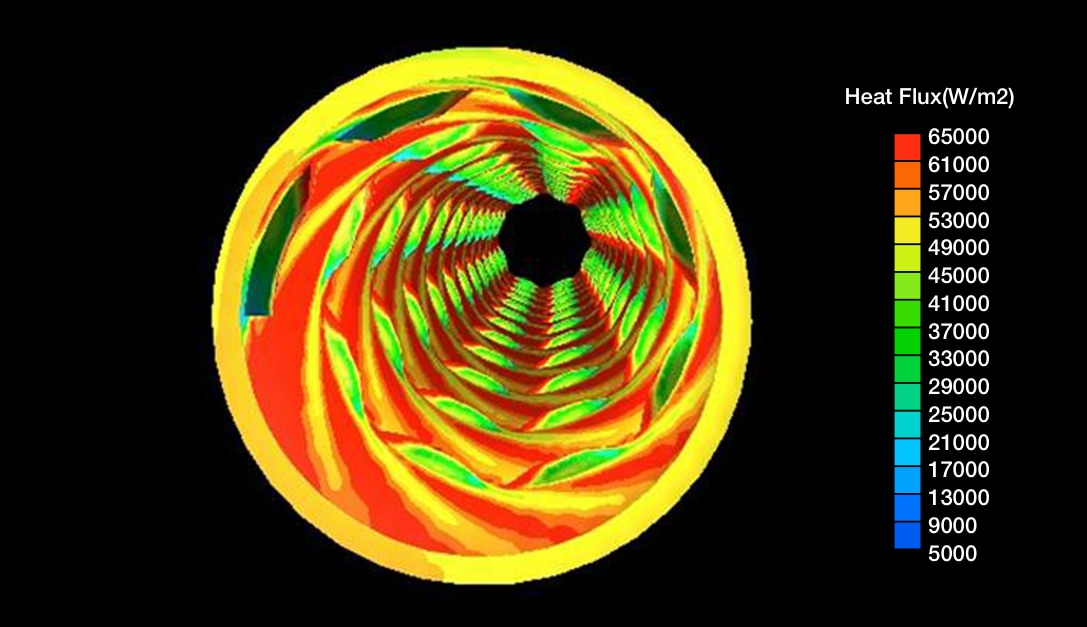
X-MERT has discontinuous mixing elements of even shorter length, which mix the fluids more evenly near the inner surface to flatten the temperature and heat flux distributions near the inside surface.
Even with a smaller element height to minimize pressure drop, it has a mixing effect and heat transfer characteristics as good as those obtainable with MERT and Slit-MERT.
Installations
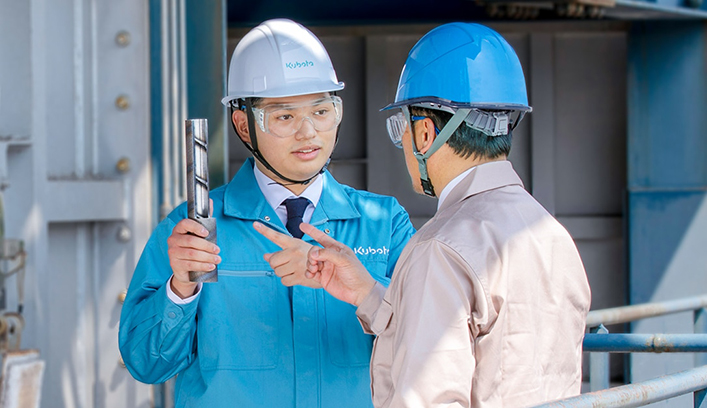
Since its launch in 1996, MERT has been installed in 857 furnaces at petrochemical plants around the world. From Kubota's lineup of high-performance products, we can recommend the ideal cracking coil for your furnace.
- Number of installations (at the Dec. 2023)
-
- MERT:324
- Slit-MERT:356
- X-MERT:177
Technical Support
- Proposals Using the Simulator to Analyze Thermal Cracking Furnaces
- Using the de facto industry-standard thermal cracking furnace analysis simulator SPYRO®, we can quantitatively predict the benefits that you will gain from using our high-performance cracking tubes, including the MERT series, which allows us to propose a cracking coil design that is optimal for your furnace type and furnace operation conditions.
- Offer of Remaining Life Assessment Service & Kubota Carburization Detector
- We can measure the levels of carburization in your cracking tubes using a testing device made by Kubota, and assess the remaining life of your tubes to help you plan renewals.
Related Products
Cracking Tubes (Cracking Coils)
Cracking tubes are used in the manufacturing processes for ethylene and propylene, which are the raw materials of petrochemical products.
AFTALLOY
AFTALLOY is a next-generation, high-performance cracking tube with a robust inert aluminum oxide layer on the inside surface.
Related Technologies
Surface Modification
The chemical composition or structure of a material surface is altered through special treatment to add a new function to the base material.
Contact Us
To inquire about a product, service, maintenance, or any other matter, please contact your nearest Kubota location directly by phone or contact us by email. Before making an inquiry, we recommend that you check out our customer support information, including FAQs, as you might be able to find the answer to your question more quickly there.