Technologies & Products
Kubota's materials
support industries worldwide and contribute to the development of society
Over many years, we have always brought more thinking to bear on our customers' problems than
they have themselves and, in every case, we have solved them. In the process, we came to develop
and acquire technologies and products that make us different from others. These capabilities have
made us first choice for manufacturers and construction companies worldwide, have created new
values, and contribute to the development of industry and society.
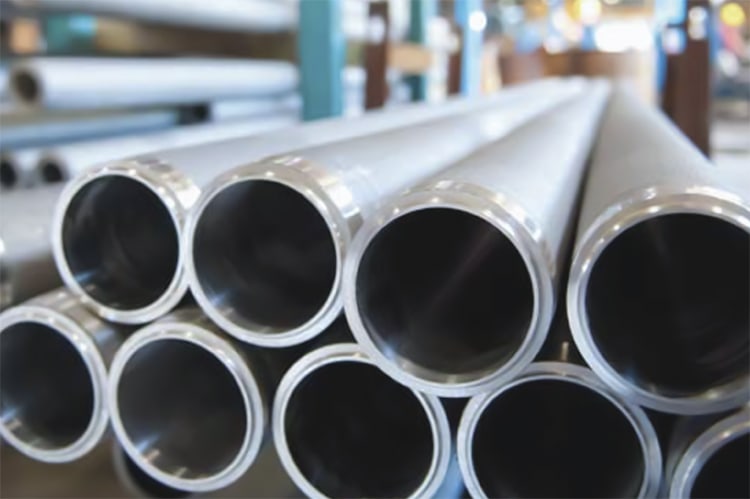
Kubota's heat-resistant alloy productswith diverse characteristics
Kubota's heat-resistant alloy was first developed for reformer tubes used in petroleum refining plants. Today, after more than 50 years of relentless study, we have realized a steel material with industry-leading heat resistance that is usable under high temperatures up to 1300°C. In addition to the high heat resistance, it can be given other characteristics such as resistance to oxidation, carburization or thermal shock in a temperature range between 900°C and 1300°C, according to customer requirements.
Metallic materials engineering enables materials with tailor-made characteristics to be designed
We have the technological expertise to design metallic materials, including heat-resistant alloy materials, imbued with a variety of characteristics to meet different market needs. We can design a broad range of metallic materials, examples of which include those with carburization resistance and high creep strength for use in petroleum refining plants, those with high compressive strength for use by the steel mill industry, low or medium alloy steel materials.
Kubota's cracking tubes and reformer tubes command the biggest market share in Japan
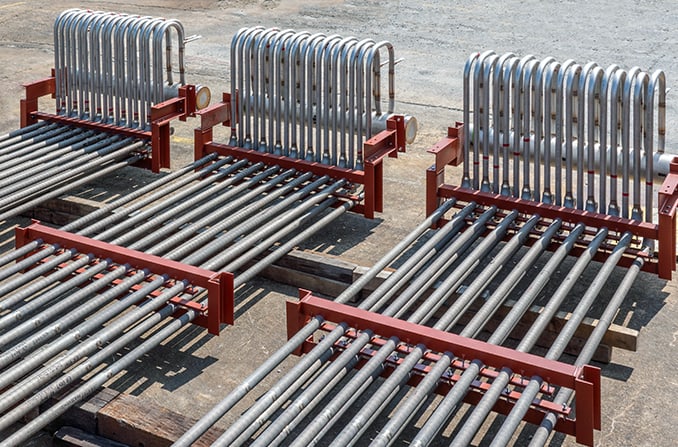
Cracking tubes and reformer tubes, which are used mainly in petrochemical plants, petroleum refining plants and fertilizer plants, need to be made of a material that can endure high temperatures and pressures. Kubota's heat-resistant alloy cracking tubes and reformer tubes that are able to withstand such extreme conditions are one of our mainstay products and are chosen by many industry users. Their high quality and reliability are proven by the leading position they have maintained in the domestic market.
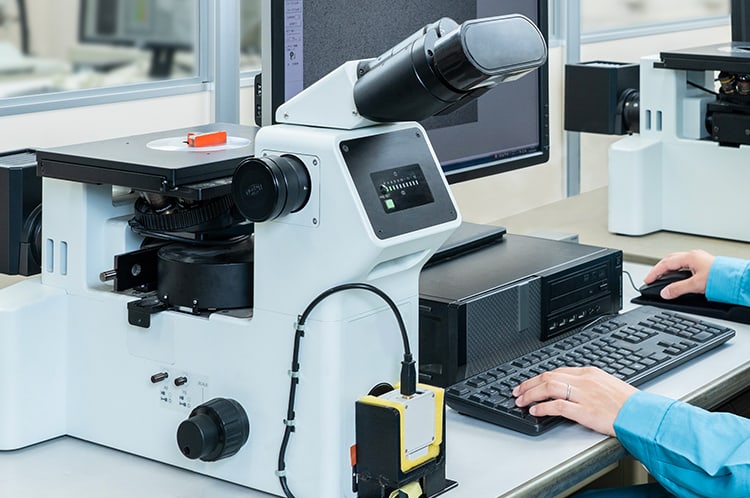
A wide range of raw material variationsto achieve an optimal balance between performance and cost
The wide range of materials we can offer is one of our strengths, from Kubota's proprietary high-grade materials to cost-effective ones, including metallic and non-metallic types. Rather than just recommending expensive high-quality materials to all, we propose materials appropriate for the budget of each customer, based on experience, knowledge and technical expertise developed over many years. This approach has resulted in successes even beyond customer expectations, and the large range of material variations that we offer.
UCX: Kubota's proprietary material born out of the pursuit of better heat resistance
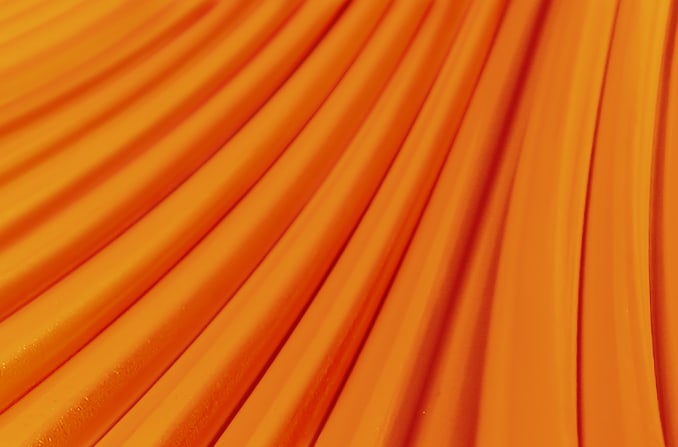
UCX is Kubota's proprietary high-grade material developed utilizing the technological expertise in alloy design that we have accumulated through studying heat-resistant alloys for many years. The material developed for cracking coils exhibits high resistance to carburization and oxidation under elevated temperatures in excess of 1100°C. It has been used at petrochemical plants in North America and many other facilities around the world.
TXAX: ceramic material with infinite possibilities
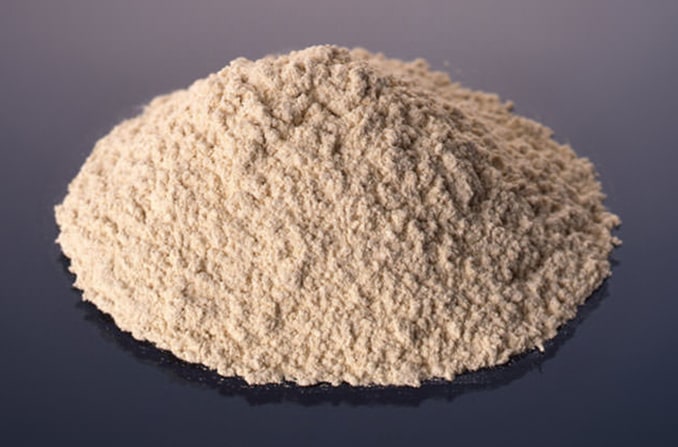
TXAX is a ceramic material with high functionality and safety which was developed and commercialized by Kubota based on the results of a collaborative research project with the National Institute for Research in Inorganic Materials (NIRIM), then affiliated to the former Science and Technology Agency.
Having high heat resistance, good thermal insulation under high temperatures, high wear resistance and high friction stability, TXAX today is primarily used for automobile brake pads. Other applications include plastic composite materials and functional paints. This is attracting considerable attention as a material that has potential to create new market values.
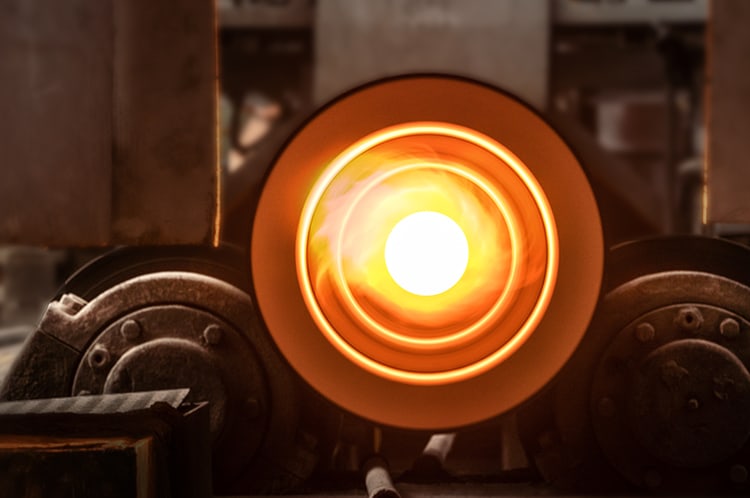
Process technologiesto realize products with advanced functions and added values
As market needs diversify and higher-level requirements increase in concert with industrial development, the standards of quality and performance required of industrial materials is becoming increasingly high. With the process technologies that have been refined over some 130 years based on casting technologies, which are the roots of Kubota, we realize products with high added values to meet high-level customer requirements.
Among other things, we are especially adept at incorporating a special process such as surface modification into the conventional manufacturing process for making high-quality castings, to realize products with advanced functions and values which meet highly specialized customer requirements. Your manufacturing activities will certainly be assisted by the technological expertise available only from Kubota.
MERT: proprietary product embodying Kubota's strengths
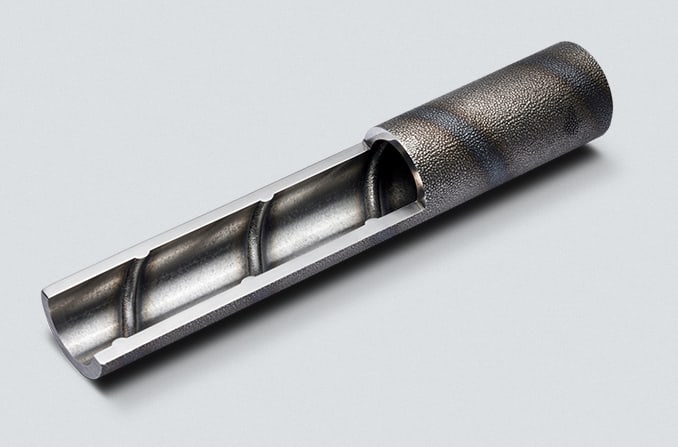
MERT is a cracking tube developed independently by Kubota. Agitation of fluid gas in the tube by "mixing elements" provided on the tube’s inside surface increases heat transfer while realizing uniform temperature distribution inside the tube; this can dramatically boost operation efficiency of cracking furnaces. The unique concept of providing a mixing element through overlay-welding on the tube’s inside surface, and the technological and technical expertise which gave form to the concept, are perfect examples of our strengths. This is one of the products that symbolize Kubota's industrial materials business, based on our materials development and process technologies as well as the experience and knowledge that we have accumulated over many years.
AFTALLOY: new-generation cracking tube
developed based on Kubota's surface modification technologies
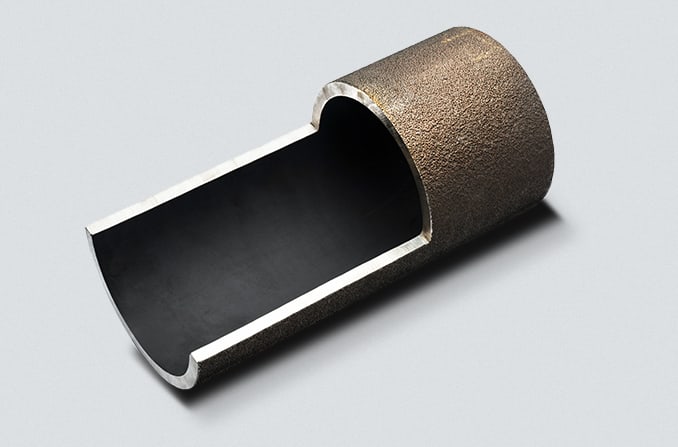
AFTALLOY is a cracking tube with an alumina layer on the inside surface. It can dramatically boost the operation efficiency of cracking furnaces and tube life. This has been developed based on Kubota's surface modification technologies. The alumina surface formed by means of a special process on Kubota's heat-resistantalloy, which is resistant to peeling, dramatically increases resistance to carburization, oxidation and coking, while the base material itself has high heat resistance. This is a product that could only have been realized with Kubota's advanced process technologies.
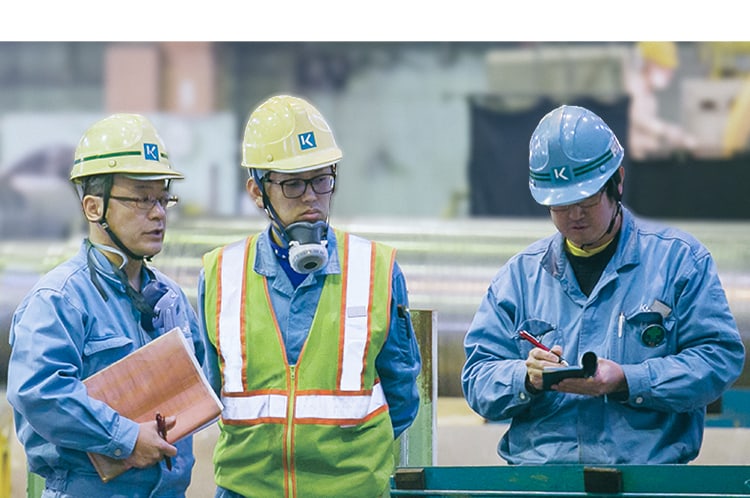
One-stop shop with all functionsto flexibly meet customer requests
Another important element that is essential for us is our organization, which makes us better than others at solving customers' problems by proposing optimal combinations of materials and technologies based on past experience and accumulated knowledge. Even if we had all of the required experience, materials and technologies, it would be impossible for us to give form to customers' requests without an organization that enables us to use these strengths effectively.
All of Kubota's industrial material products are made in-house throughout all stages, from research on raw materials and materials development through manufacturing and inspection, so that we can take full advantage of our strengths. This facilitates team efforts across different functions and makes it easier to respond flexibly to customer requests in each process.
Steel pipe sheet pile with Laqnican Joint
realized through team efforts across departments
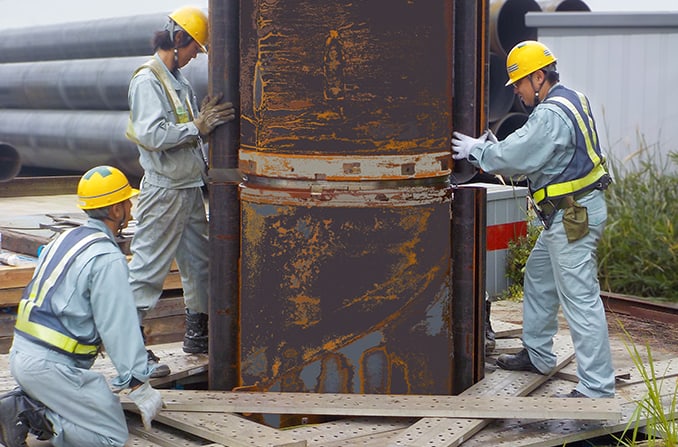
In conventional construction methods, steel pipe piles or steel pipe sheet piles were jointed by field-welded steel tubes delivered to the construction site. However, Laqnican Joint, a mechanical joint developed as an alternative to field-welding, had already recorded several successful uses in steel pipe pile applications. Steel pipe sheet piles for use with mechanical joints were considered difficult to commercialize because there were serious challenges in terms of manufacturing technology.
Under these circumstances, we received strong customer requests to realize a "shorter construction period" in construction projects through use of steel pipe sheet piles. We set up a project team comprising personnel from the R&D, sales and manufacturing functions, to solve difficult problems we faced, bringing together the knowledge and technical expertise from different sections. Team members conducted many discussions and much trial-and-error experimentation. The team eventually managed to solve those challenges through their efforts and realize commercialization of steel pipe sheet piles with Laqnican Joint, which had formerly been seen as difficult. By drastically shortening the time required for jointing steel pipe sheet piles on-site, we offered a new value to the market, a "shorter construction period."
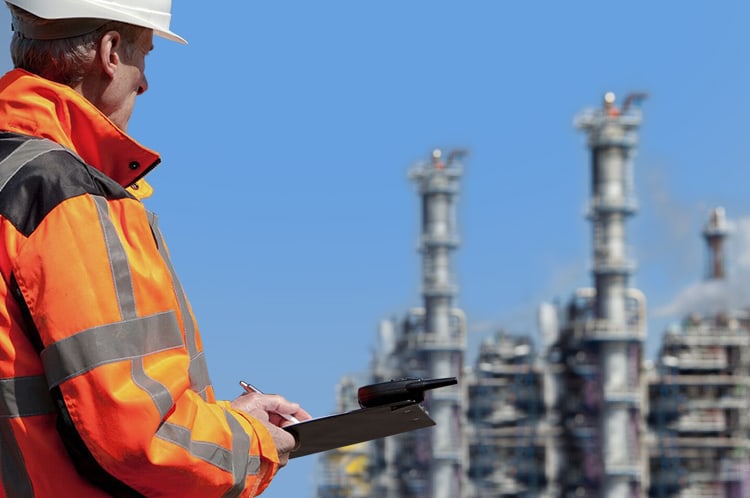
Kubota's industrial materialschosen by industries worldwide
We bring more thinking to bear on customers' problems than they do themselves and we solve them by proposing optimal combinations of materials and technologies based on our long-accumulated experience and knowledge. As a result of this approach, which is integral to every product we make, gaining acceptance both within and outside of Japan, Kubota's industrial materials now play vital roles on manufacturing and construction sites around the world.
For example, in the petrochemicals industry, Kubota's cracking tubes and reformer tubes maintain a large share of the global market.
Kubota tops the global cracking tubes market
Cracking tubes used in petrochemicals plants are required to be of very high quality among heat-resistant products because they require high heat resistance and other characteristics such as corrosion resistance. Kubota's cracking tubes have the largest share of the global market, having been chosen by many petrochemical industry users, both within Japan and overseas.