04
KUBOTA in U.S.A.
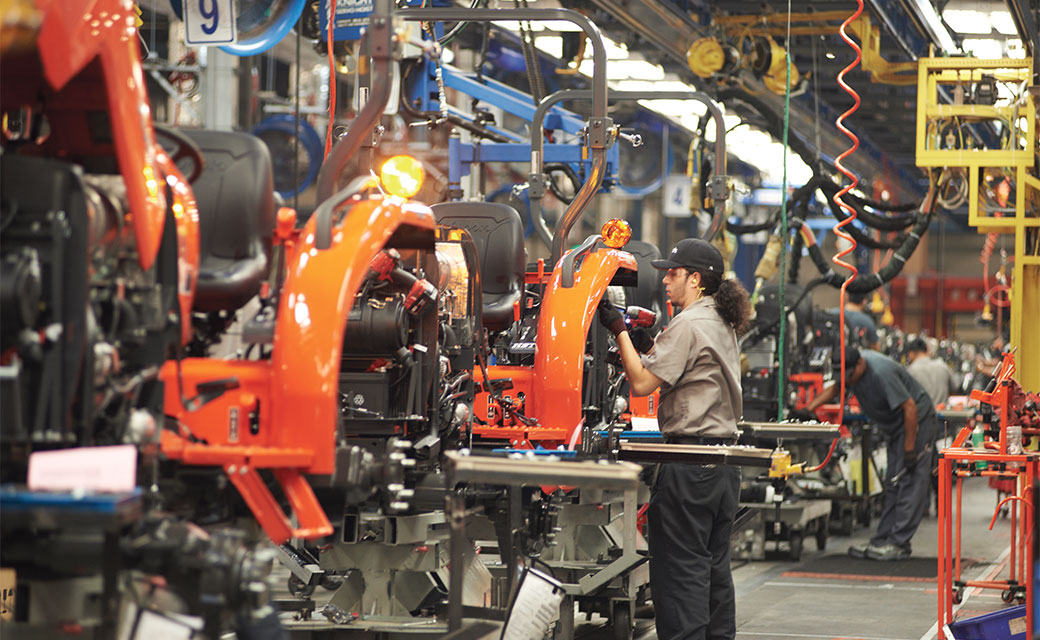
Business
The globalization of manufacturing The opening of a North American “5-Gen Dojo”
“5-Gen” is the three principles of “GENBA (Actual Sites), GENBUTSU (Actual Objects) and GENJITSU (Facts)” and the two principles of “GENRI (Principles) and GENSOKU (Basic Rules).” The way of thinking of the “5-Gen” principles is to clarify the difference between these first three “Gen” (= the current level) and the second two “Gen” (= the ideal situation according to the principles and rules) and to correctly understand the nature and the cause of a problem. Improvement activities based on the “5-Gen” principles are implemented at the sites of manufacturing. The activities are developed to determine what is wasteful in the work and to thoroughly remove it to raise productivity. Please imagine a scene of manufacturing within a factory. At the assembly workplaces, waste is anything other than the instant when workers are fitting parts or tightening bolts. In other words, anything other than the action of adding function to a product is waste and reduces productivity. Furthermore, all products not immediately required by customers and all goods in process that are not being worked on are waste.
The “5-Gen Dojo” puts the ideas of this “5-Gen” principle into practice in a training program developed for manufacturing personnel. The training school started out at the Sakai Plant in Osaka, Japan in 2002 and to date more than 2,000 employees have received the training. In 2014, the first school at an overseas base was opened at Kubota Manufacturing of America Corporation (KMA). The “5-Gen Dojo” at KMA has an American person as the acting master (instructor) and the students are able to receive the course in English. Local instructors are able to nurture the local personnel autonomously. Together with that at the Sakai Plant, the “5-Gen Dojo” at KMA will play an important role in the global expansion of the “5-Gen” principles.
-
Kevin Strike and the rest of the “5-Gen Dojo” secretariat are incorporating improvements typical of KMA as they promote it.
Kevin Strike, who works in the administration of the “5-Gen Dojo” at KMA said: “First we must increase the number of personnel that have a foundation in the “5-Gen.” At the present time we run a program with 12 students four times a year. Everybody feels that it is a place to learn a good way of thinking and we have certainly seen the results of it. In the future, I would like to increase the number of acting masters in the teaching position. When this happens, the graduates of the North American “5-Gen Dojo” and the acting masters will be able to come together and incorporate the 5-Gen ideas into the production workplaces. Actually, we set three model processes in the workplace per month and implement improvement support. Even so, it will probably take 2 or 3 years for improvement at each workshop independently. In the future, I hope that we will accept trainees from bases around the world at our Dojo. Our objective is not for the Dojo to become established. It is for the culture of “5-Gen” improvements to become established over the long term.”
Towards “local production for local consumption” in tractors Establishment of new KIE plant (2nd plant)
As the American economy has developed and KUBOTA's line-up of products has expanded, the sales of KUBOTA tractors have grown rapidly since the late 1990s. The cumulative sales exceeded 1 million units in 2005.
At Kubota Industrial Equipment Corporation (KIE), the production of implements (work devices for attachment to tractors) began in 2005. With the establishment of this new plant (starting mass production in 2013), productivity has been dramatically improved as work such as the attachment of implements and tires and the production of tractors has been concentrated in one place. On top of this, the local production reduces the risks from foreign exchange fluctuations. The cost competitiveness has also been strengthened through “globally optimum procurement” performed by purchasing the key parts from production bases in Thailand, etc., in addition to from Japan. At present, between 80 and 90 tractors are produced per day at the new plant. The latest IT techniques have been introduced such as the computerization of all the quality data and the displaying of failure information on screens.
In addition, the new plant has a wastewater treatment facility containing the KUBOTA Submerged Membrane and is reusing its wastewater. The contaminants in the plant wastewater and domestic wastewater are separated off and 65% of the wastewater is reused in coating processes. The remaining 35% is purified beyond the required level and drained as sewage. Furthermore, the coating processes include processes which require “ultrapure water” and a high precision RO (reverse osmosis membrane) has also been installed and is contributing to increased rates of wastewater recycling.
-
The newly established KIE 2nd plant A quicker response has been realized by locating the production close to the sales market.
Environment
The development of diesel engines to meet the latest emissions regulations
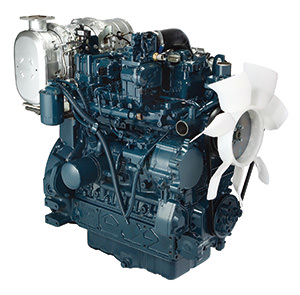
An awareness of the environment is strong in the advanced nations of Europe and America and regulations related to “exhaust gas” are especially strict. In the U.S, the “Tier 4 emissions regulations” are being introduced in sequence. To survive in the American market, every product from passenger vehicles to agricultural machinery and construction machinery must be an environmentally friendly product.
In 2011, in advance of the Tier 4 emissions regulations, KUBOTA became the first company globally to obtain certification from the U.S. Environmental Protection Agency and the California Air Resources Board for compliance with the emissions regulations (for the 56 to 130 kW class). Certification of compliance for the 56 kW and smaller class was also achieved for all series in 2012 and so the response to the regulations was completed in that same year, when the regulations were begun. We have also completed development of an engine to comply with the Tier 4 final emissions regulations to be implemented in the U.S from January 2015 and certification has been obtained.
By receiving this certification, we are able to launch models that support the emissions regulations when they are ready and we have increased our business opportunities regarding OEM sales of diesel engines. KUBOTA is already a top manufacturer of small diesel engines for industrial use. The company also continues to be a leading company in environmental issues.
Water
The latest earthquake resistant ductile iron pipe “GENEX” is being used in Los Angeles
The west coast of America is a region that has many earthquakes. In the City of Los Angeles in California, the improvement of water pipelines against earthquake is a major issue and measures had been discussed for many years. In 2013, the City decided on the trial adoption of earthquake resistant piping made in Japan. Those pipes were the KUBOTA “GENEX” earthquake resistant ductile iron pipe for waterworks. It was the first time that water pipes with Japan's unique earthquake resistance performance had been used in the U.S.
In the background to that selection were the proven results with earthquake resistant pipes in Japan. The characteristic feature of earthquake resistant ductile iron pipes is that even if an earthquake occurs, the joints between the different pipes expand and contract and also deflect at the joints. The joints do not fall apart even if a strong force is applied, like on a chain. The effectiveness of these earthquake resistant pipes was proven in the Great Hanshin Earthquake (1995) and the Great East Japan Earthquake (2011). There was no damage even where the land subsided or cracked open. “GENEX” is the latest model of earthquake resistant ductile iron pipe with improved workability and corrosion resistance on the outside. In Japan today, earthquake resistant pipes are used for roughly 90% of the newly installed ductile iron pipe for water suply. These proven results were also highly evaluated in America.
The region where the trial installation was performed was a region that suffered damage in the Northridge earthquake of 1994 and landslides have also been confirmed. KUBOTA products are supporting the residents' safety and peace of mind from under the ground.
-
Trial introduction has also begun outside of California in places such as the State of Oregon. We will continue to use the proven results in Japan to try to spread the piping throughout America.
The “KUBOTA Submerged Membrane Unit®” in service at more than 300 wastewater treatment plants in the U.S
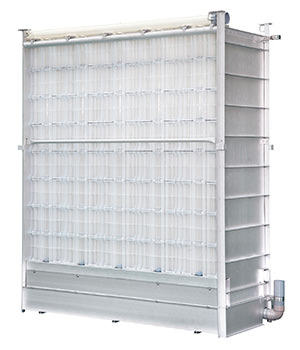
The environment surrounding KUBOTA's wastewater treatment business in the U.S is improving. An increase in demand to retrofit aged wastewater treatment plants, a strengthening of nutrient removal of nitrogen and phosphorous to improve water quality as well as the need of wastewater reuse to overcome water shortages have been observed. In addition, the housing starts index is again above the 1 million per month mark as the economy recovers.
Kubota Membrane USA (KMU) has recently incorporated their product lineup with designing, integrating and supplying the MBR (Membrane Bio Reactor) system based on the wastewater treatment engineering capability, know-how and experience over the many years at KUBOTA in Japan in addition to supplying just the submerged membrane unit. KUBOTA's ability to design the entire system enables our membranes to perform in operation with full optimization. The first KUBOTA MBR system is being installed in the state of Washington where KMU is located. The KUBOTA MBRs have garnered significant attention because of KUBOTA's design know-how and over 300 wastewater treatment plant references using our submerged membrane units in the U.S.
In 2013, the order from the City of Canton for the MBR water reclamation facility which is the largest MBR in North America was awarded in cooperation with a partner company.